Leading Edge August 2021
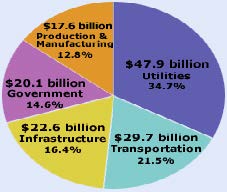
Project: Clarifier Tank Repair and Upgrade
One of North America’s largest flat role steel producers had a clarifier at its continuous caster was starting to leak and needed a long-term repair.
The customer was concerned about possibly blasting through the substrate in badly corroded areas. This concern restricted our surface preparation options. We opted to use NACE #3/SSPC- SP-6 commercial blast vs. NACE 1 or 2. We applied Maxon CRS as a steel primer to insure proper adhesion due to the commercial blast. We then applied Duromar SAR, a ceramic metal repair to build up and repair and strengthen damaged steel thus avoiding hazardous welding and brazing. We then applied Duromar RPL DF-1303, a Zero VOC to prime the concrete floor and repairs made with Duromar RPC, a 100% Solids, Zero VOC concrete resurfacing compound.
Did you realize corrosion cost for the USA is $1.1 Trillion per year? This is according to the 2015 impact Study. Corrosion never sleeps, it is 60 second a minute, 24 hours a day, 365 days a year.
The cost of corrosion in the following industry sectors in between 3.5 to $14 Billion a year each. The costs of corrosion come in form of either premature deterioration or failure resulting in the need for maintenance, repair and replacement of damaged equipment. Others sources of cost come from lost production and increased downtime of equipment arising from corrosion problems.
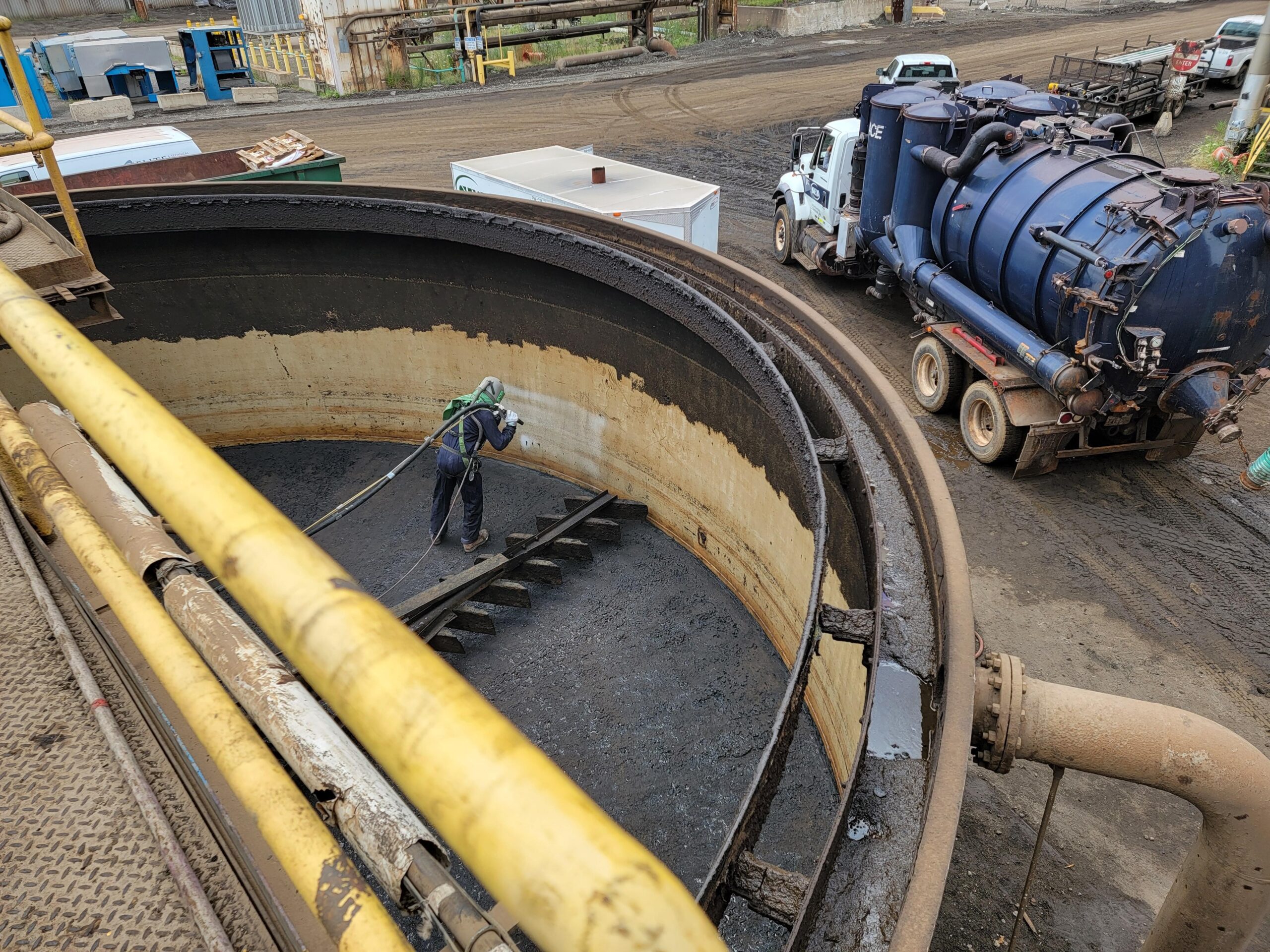
We then applied Duromar HPL 1110-F, a high performance, multi- functional lining, as the liner to protect the steel, concrete, and the chime area of the clarifier and to prevent further corrosion in the internal chime area. The clarifier was coated 3 feet up the steel and 3 feet on the concrete floor. The entire project was completed in 2 – 16 hour shifts of the scheduled 72-hour outage, thus allowing the coating to properly cure for 12 hours before returning the clarifier to service.
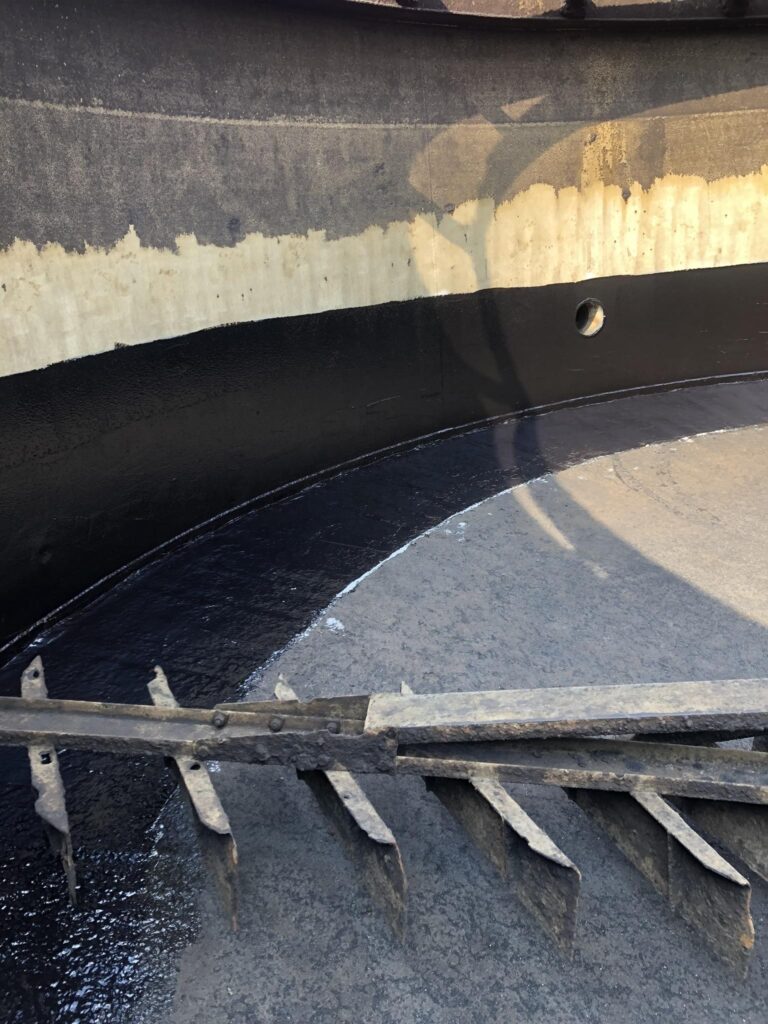
USI Dates To Remember!
Central NACE Kansas City, KS Aug 4-6th
Denso Webinar Benefits of Viscotaq Aug 12th
KGA Lexington, KY Aug 24th & 25th
Purdue Underground Corrosion Fort Wayne, IN Aug 31st-Sept 2nd
Did you know? USI can come help train and educate!
The USI Team can train your team safely on site, in person, if wanted, on many products! We can also train remotely via video or conference calls and walk you and your team through procedures ahead of time or live talk through while you make the repairs.
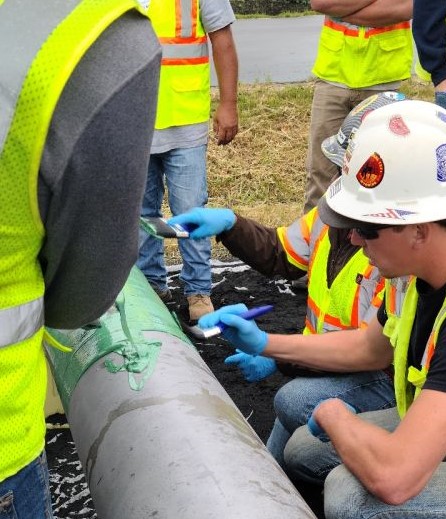
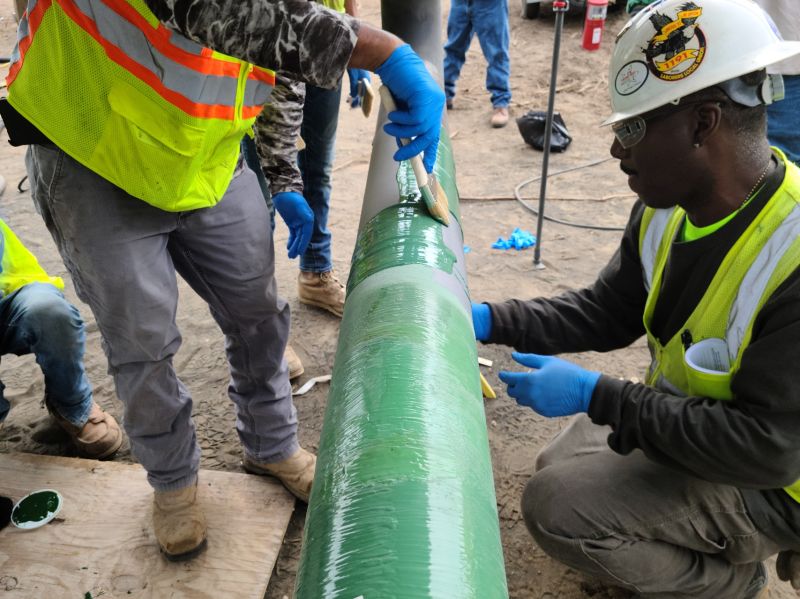
We can also do “Lunch and Learns” and Doughnut Demos.
Let USI help, we have customized solutions to help you meet and exceed your goals.
Contact the USI Team at 248-735-7000 and schedule your teams training today!
USI’s FEATURED PRODUCT
HPL-1110 is a flexible, low viscosity, easy to use coating system used on structural steel, tank exteriors or other areas where extra corrosion resistance is required. It is shipped DOT non-corrosive.
Force cures can be used to accelerate the cure or to enhance both physical and chemical properties. Force curing should not start until material has firmly set. Contact USI for specific instructions.
CONTACT THE USI TEAM TODAY!
We have an Unconventional Solution for YOU!
MICHIGAN HQ
office@USIgroups.com
248-735-7000
NW Indiana Branch
nw-inoffice@USIgroups.com
219-733-0543
SW Ohio Branch – Jason
daywh@USIgroups.com
937-704-4220
Account Manager – Jerry
Jerry@USIgroups.com
315-497-1072
cell 315-283-3906
Agriculture Facility Maintenance Manufacturing Mining / Minerals / Metals Power Refinery Water/Waste Water