Case Studies
For over 20 years, USI has provided protective coatings and corrosion prevention products proven to protect our nations most critical infrastructure and industrial machinery. Along the way we have documented many projects and pain points we have been able to help our partners repair, protect and upgrade.
Most Recent Articles
How to Plate Bond in 10 Minutes
These are the alternatives to avoid the hazards of hot work and allow you to repair structures and equipment that maybe there is not enough material to weld.
Plate bonding is a cold-applied composite repair method where a metal plate is permanently bonded over damaged or weakened areas of equipment using high-performance composite repair materials.
Why choose plate bonding over welding?
Avoid Hot Work Hazards
- No sparks, no flames, making it ideal for hazardous or flammable environments
- Eliminates need for hot work permits
Minimize Downtime
- Cold-applied, fast-curing systems get equipment back online faster
- With USI’s training, maintenance teams can complete the work without bringing in a certified welder
Stronger than welds in many situations
- Excellent adhesion and mechanical strength
- Distributes stress across the bonded area without heat distortion
- Non-corrosive
How it’s done – 5 Easy Steps
Surface Preparation – Substrate and Plate
- Degrease the surface using a suitable solvent like USI’s Universal Cleaner to remove oil, grease and contaminants.
- Mechanically abrade the area using an angle grinder fitted with a coarse pad or grinding disc. USI suggests a MBX bristle blaster for the best surface profile. You can also manually abrade the surface with a wire brush, sandpaper or metal file. Always follow the TDS for surface preparation.
- Remove all loose debris and clean again with solvent to ensure a clean bonding surface.
Dry Fit Check
- Position the plate over the damaged area and mark its placement
- Ensure proper alignment, surface contact and accessibility for application
Product Mixing
- Select the appropriate Resimac product based on the application (Resimetal 101, Resimetal 104 XF, Resimetal 106 XF)
- Mix the base and activator thoroughly until a consistent color and texture are achieved in the trio on the TDS.
Application
- Apply a uniform layer of mixed product to both the substrate and the back of the plate
- Use a trowel or spatula to ensure even coverage and eliminate air pockets
- Firmly press the plate into position, sliding slightly to seat the bond.
Clamping (if required)
- Apply mechanical pressure using clamps, weights or magnets to hold the plate in place during cure (especially for vertical or overhead surfaces)
- Maintain pressure according to cure time guidelines
Curing
- Allow the repair to fully cure before returning to service
- Cure time varies by product and environment but typically ranges from 6 to 24 hours
- For faster returns to service, optional heat curing may be used if appropriate
Final Inspection
- Verify bond integrity, inspect for gaps or voids, and test hardness (if required)
- Optional: Apply a protective topcoat or corrosion-resistant finish. Resimac has many different overcoat protection options, each tailored to a different environment. Make sure to talk to a USI expert technical advisor to get the right coating for your environment.
Make sure to view the video in its entirety to get the answers to the questions covered in the podcast:
- Can you use this system for load-bearing repairs?
- What are the most common mistakes when making plate bonding? How can they be avoided?
- What are the temperature limitations on this material?
- What are the labor time savings using plate bonding vs. hot work methods?
Unreliable Equipment Costing You Time and Money?
Unreliable Equipment Costing You Time and Money?
Get a FREE Consultation to Identify and Fix the Root Cause
Downtime, excessive energy costs, and unexpected equipment failures can cripple your productivity and profits. Our expert team of technical advisors is here to help you regain control.
What’s Included in Your Free Consultation?
Our experienced engineers will:
Assess your current maintenance processes for inefficiencies and bottlenecks
Identify potential failure points in critical systems and equipment
Provide hands-on support and training to strengthen your in-house team
The Benefits You’ll See:
Reduced unplanned downtime
Lower energy consumption
Safer, more efficient operations
Better trained, more confident maintenance staff
This is a no-pressure, no-obligation consultation. Just actionable insights and expert advice to help you get back on track.
Who Is This For?
Maintenance Managers
Plant Engineers
Operations and Production Leaders
If you’re responsible for keeping the plant running and costs down—this consultation is for you.
Book Your Free Consultation Today
It only takes a minute to schedule. Let’s uncover what’s holding your facility back and create a plan to fix it.
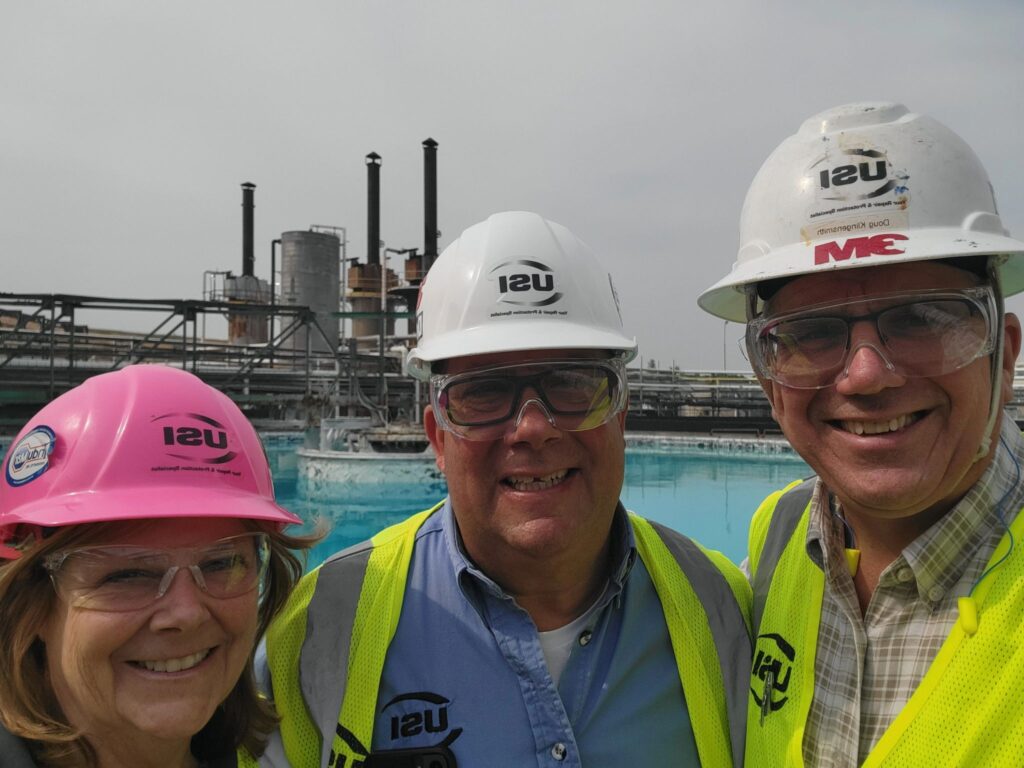
Conquer wear and tear with ceramics
Discover a reliable solution designed for industries that need a durable fix for erosion and corrosion – providing long-lasting repairs and extending the life of equipment.
https://www.usigroups.com/product-category/product-type/ceramic-repair/
Resimac 200 Series:
- Impact & Wear resistance
- Paste grade & fluid grade (good for small and bigger repairs)
- Internal applications (ie. Pumps, vessels)
- Excellent chemical protection
- Excellent heat resistance
- Application on metal surfaces underwater
- Solvent-free (no harmful smells)
- Applied with plastic spatula, applicator or brush
- Primarily for metal substrates
Case Study: Bronze Impeller Refurbishment:
https://www.usigroups.com/case-studies/bronze-impeller-refurbishment/
Case Study: Water Pump Refurbishment
https://www.usigroups.com/case-studies/water-pump-refurbishment/
Case Study: Wastewater Treatment Plant Sewage Axial Flow Pump
https://www.usigroups.com/case-studies/wastewater-treatment-plant-sewage-axial-flow-pump/
Case Study: Vertical Inline Pump for Cooling Tower
https://www.usigroups.com/case-studies/vertical-inline-pump-for-cooling-tower/