The Challenge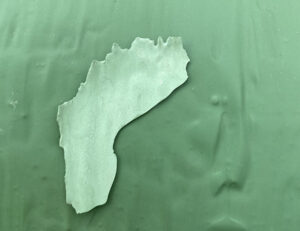
Friday afternoon – Repair Kit Coating Failure – USI Owner & President, Tiffany Klingensmith was getting ready for the weekend and got a call after 4pm. The customer said this to Tiffany, “When we started shoring the line, we found MANY jeeps. We dug up the line and where we used the repair kits, the coating was coming off the pipeline like sheets. They are a funny green color. When can you get here with your BEST Technical person?”
The Solution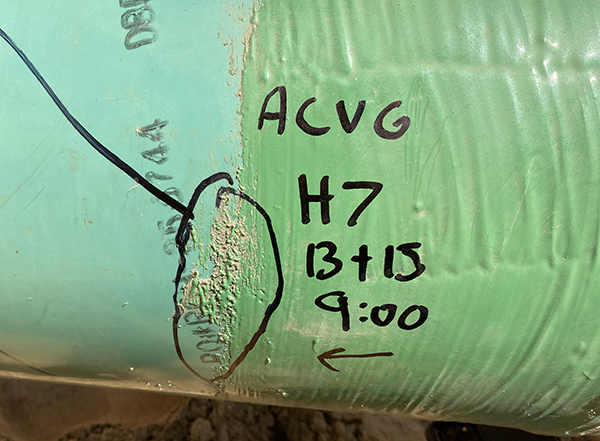
Tiffany Klingensmith went on location herself, as she is a NACE Certified Level 2 CIP and a Denso Certified Application Trainer. Once on site, she was able to troubleshoot and reinforce the contractor’s application knowledge.
Recordings must be made of the conditions, pipe temperature, dewpoint, batch numbers of parts A & B with expiration dates. When failures occur, these records are critical to determine what part of the process needs to be addressed.
The pipe surface temperature has to be a minimum of 5°F above the dewpoint and a minimum of 50°F, through the entire cure (or per manufacturer’s specifications).
Several sections were dug up for repair and re-application of the Denso Protal 7200 high-build liquid pipeline coating. The failed repairs were removed, and the newly applied patches were hardness tested to ensure a Shore D85 minimum before re-burying of the pipeline. When all of the coating manufacturer conditions are met the first time, your project coating project will be successful the first time.
Helpful hints to prevent pipeline coating failure:
- Complete surface preparation as spelled out in the product technical data sheets
- Test and record pipe surface temperature and dew point
- Multi-part components are thoroughly mixed, needs to be a homogenous color (no streaks)
- The coating achieves required hardness/cure before pipe is buried
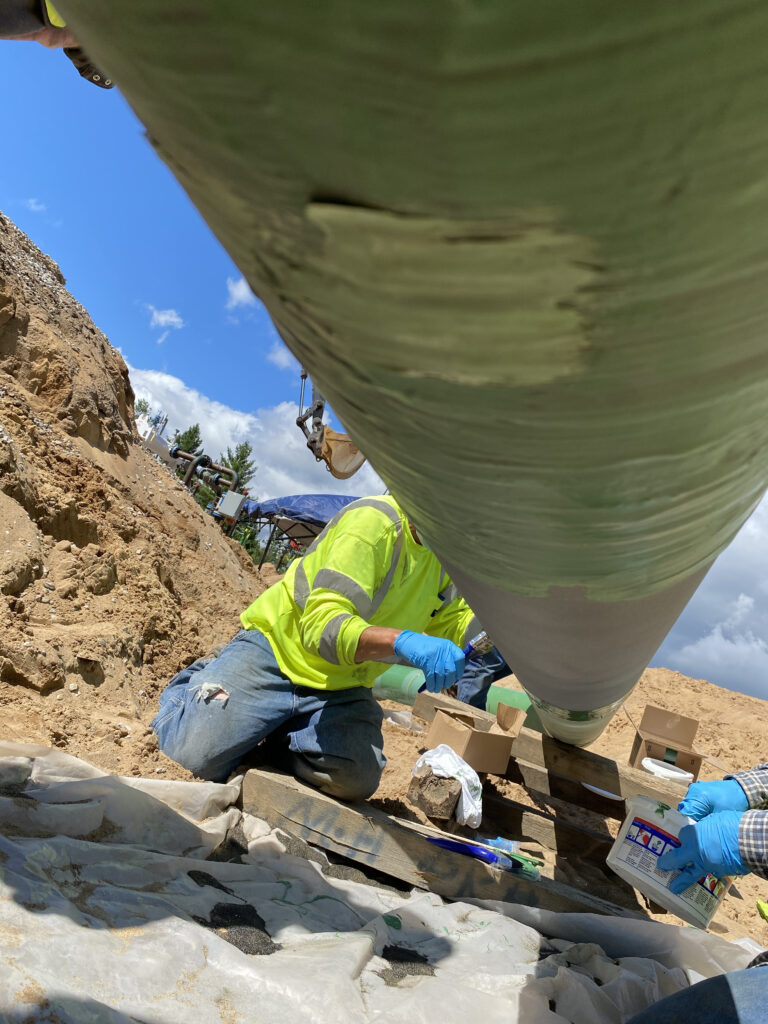