5 Reasons to Reconsider Tank and Infrastructure Repair Operations
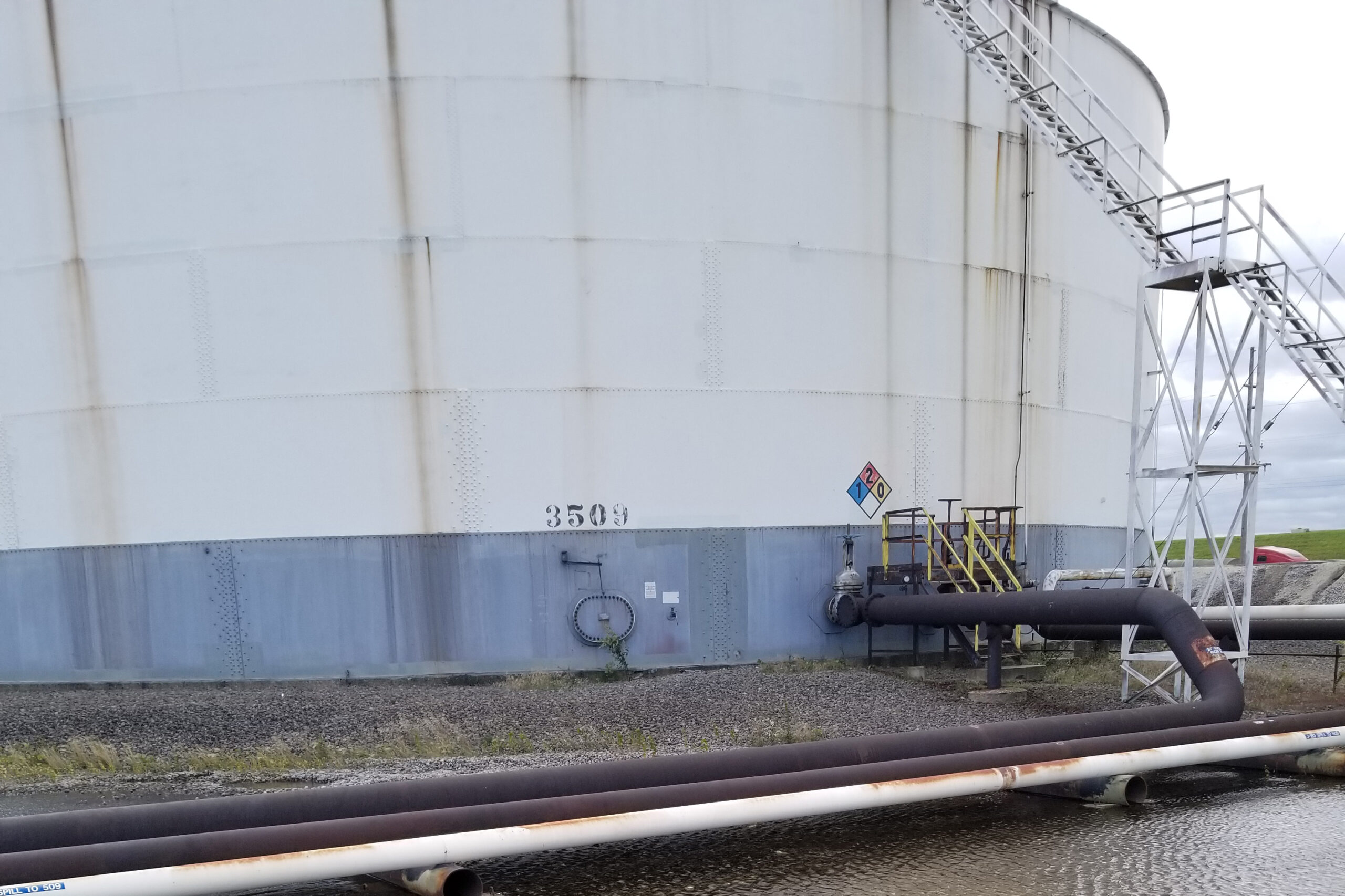
In 2021, OSHA is pushing harder than ever to reduce the number of injuries and fatal accidents contributed directly to welding and has labeled it a “high priority” in its operations.
The US Bureau of Labor Statistics declared that welding poses unique risks to over 500,000 workers due to explosions, falls, crushing, electrocutions and asphyxiations. (www.wcwelding.com)
With these grim realities, you need additional repair options to keep your operations safer and more efficient. USI is partnering with oil & gas professionals to:
- Lower your overall maintenance cost and improve reliability
- Avoid hazardous “Hot Work”, and eliminate corrosion cells caused by welding
- Utilize the entire workforce with easy to use “cold weld” alternatives with simpler and faster maintenance procedures
- Extend the life of fixed equipment, structures, rotating equipment, and machinery
- Reduce and postpone capital expenditures
The more innovative companies in your industry are repairing, protecting, and upgrading their equipment and infrastructure with Resimac Epoxy coatings for:
- Corrosion protection
- Tank repairs at rivets, welds, and roof
- Chemical tank lining
- Tank base sealing
- Thermal coatings to improve personal protection and avoid burns
- ASME PCC2 long-term and temporary repairs to extend pipe life
- Corrosion under insulation (CUI) prevention
At USI Groups, we have already partnered with the following companies to address their issues with proven solutions from the Resimac products:
- BP – Whiting, IN Refinery – Riveted tank repair to avoid OSHA fines until tank could be replaced
- Buckeye Pipeline – Marshall, MI – Pipe Repair on 3-inch coupling leak
- Citgo – Arlington Heights, IL – Leaking oil pipe fixed without “Hot Work”, improving safety
- Enbridge – Griffith, IN – Floating roof repair to avoid expensive replacement and EPA fines
Additionally, we provide technical support, training and troubleshooting to help you succeed with your repair projects. This article is your invitation to the same innovations for your company. Click on the link below for immediate shipment of Resimac to your facility.
You can also reach out to us at (248) 735-7000 for more information, to process your order, or to make an appointment for a site visit or training. Either way, it is our privilege to serve you and we look forward to a long-term relationship with you.
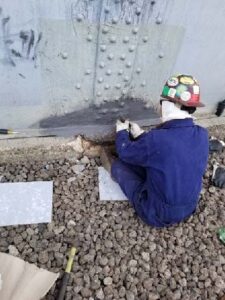
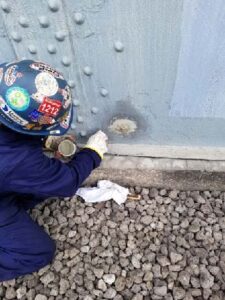
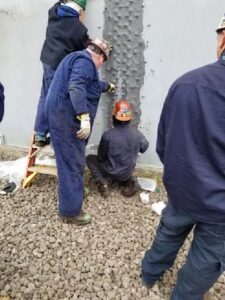
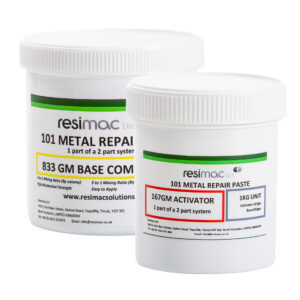
Resimetal 101 Industrial Epoxy Metal Repair Paste/Glue
Resimetal 101 Industrial Epoxy Metal Repair Paste/Glue is a two component solvent free epoxy metal repair compound designed to fill surface erosion & corrosion on metallic surfaces. The material can be applied to mechanically or abrasive blast cleaned surfaces and once cured will retain high mechanical adhesion to metallic substrates. The thixotropic nature of the product means it can be applied at thicknesses up to 25mm without sagging and can be machined to fine tolerances.
Resimac Resimetal 101 industrial epoxy metal repair paste/glue typical applications:
-
- Worn or damaged pump shafts
- Worn bearing housings
- Worn keyways
- Cracked pump or valve casings
- Damaged flanges
- Cracked engine blocks
- Scored hydraulic rams
- Leaking Tank Seams
The Resimetal 100 series products are capable of repairing a wide range of metal components. The full series is described in brief below, if you need more details please navigate to that product linked below.
Resimac Resimetal Metal Repair Product Range
101 Metal Repair Paste – High build engineering grade repair paste – Current Product!
103 Metal Repair Stick – Fast curing putty for emergency repairs
104 Metal Repair Fluid XF – Fast curing fluid for application to oily surfaces
105 Aqua Stick – Fast Curing putty for underwater repairs
106 Metal Repair Paste XF – Fast curing engineering grade repair paste
108 Pipe Repair Tape – Rapid curing moisture activated repair bandage
Frequently asked Questions:
How brittle is it?
Has a flexural strength of 10,000psi and a compressive strength of 15,3000psi.
How does it do with heat?
Suitable for water immersion up to 158°F and intermittent contact with steam up to 248°F. Dry heat resistance up to 392°F.
Will it adhere to PVC?
Yes, it will adhere to PVC as long as you prepare the surface properly
What is the cure time?
At 68°F it is touch dry in 1 hour and machinable in 2 hours.
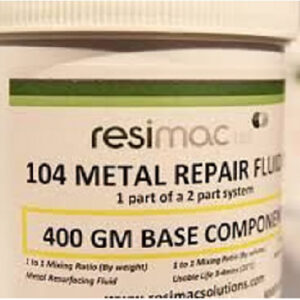
Resimac Resimetal 104 XF Metal Repair Fluid
Resimac Resimetal 104 XF Metal Repair Fluid a two component solvent free fast curing epoxy repair fluid. The product has been designed to be applied to surfaces where only manual or mechanical surface preparation can be performed and to surfaces contaminated with low viscosity oils and lubricants.
FEATURES
- Solvent free epoxy technology
- Brush or applicator tool applied
- Apply to manually prepared surfaces
- Apply to oil contaminated surfaces
- Fast cure – hard dry in 45 minutes
- Approved by NWEL for onsite transformer repairs
TYPICAL APPLICATIONS
- Leaking Pipe Joints
- Leaking Tank Seams
- Transformer Repairs
- Leaking Flange Fittings
- Anti slip coating for metal decks and stairs
- Resurfacing of corroded steel plates
The Resimetal 100 series products are capable of repairing a wide range of metal components. The full series is described in brief below, if you need more details please navigate to that product linked below.
Resimac Resimetal Metal Repair Product Range
101 Metal Repair Paste – High build engineering grade repair paste
103 Metal Repair Stick – Fast curing putty for emergency repairs
104 Metal Repair Fluid XF – Fast curing fluid for application to oily surfaces – Current Product!
105 Aqua Stick Fast – curing putty for underwater repairs
106 Metal Repair Paste XF – Fast curing engineering grade repair paste
108 Pipe Repair Tape – Rapid curing moisture activated repair bandage
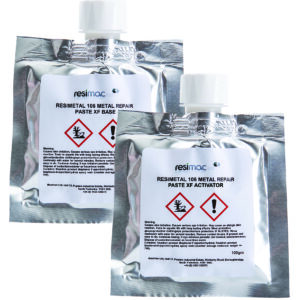
Resimac Resimetal 106 XF Metal Repair Paste
Resimac Resimetal 106 XF Metal Repair Paste is a fast curing two component solvent free epoxy metal repair compound. The product has been designed for use on a wide range of metallic surfaces and once cured is readily machinable.
FEATURES
- Solvent free epoxy technology
- 5 minutes usable life
- Fully cured in 60 minutes
- Bonds to any metal surface
- Applied by spatula or applicator tool
- High build capability (1″ without slumping)
- Can be applied underwater
- Apply to manually prepared surfaces
- High mechanical strength
Resimac Resimetal 106 XF Typical Application
- Damaged Pump Shafts
- Leaking Tank Seams
- Underwater Hulls
- Cracked Pump or Valve Casings
- Cracked Engine Blocks
- Underwater Structures
- Damaged Flanges
- Underwater Surfaces
The Resimetal 100 series products are capable of repairing a wide range of metal components. The full series is described in brief below, if you need more details please navigate to that product linked below.
Resimac Resimetal Metal Repair Product Range
101 Metal Repair Paste – High build engineering grade repair paste
103 Metal Repair Stick – Fast curing putty for emergency repairs
104 Metal Repair Fluid XF – Fast curing fluid for application to oily surfaces
105 Aqua Stick Fast – curing putty for underwater repairs
106 Metal Repair Paste XF – Fast curing engineering grade repair paste – Current Product!
108 Pipe Repair Tape – Rapid curing moisture activated repair bandage