5 Water Projects to Consider this Spring
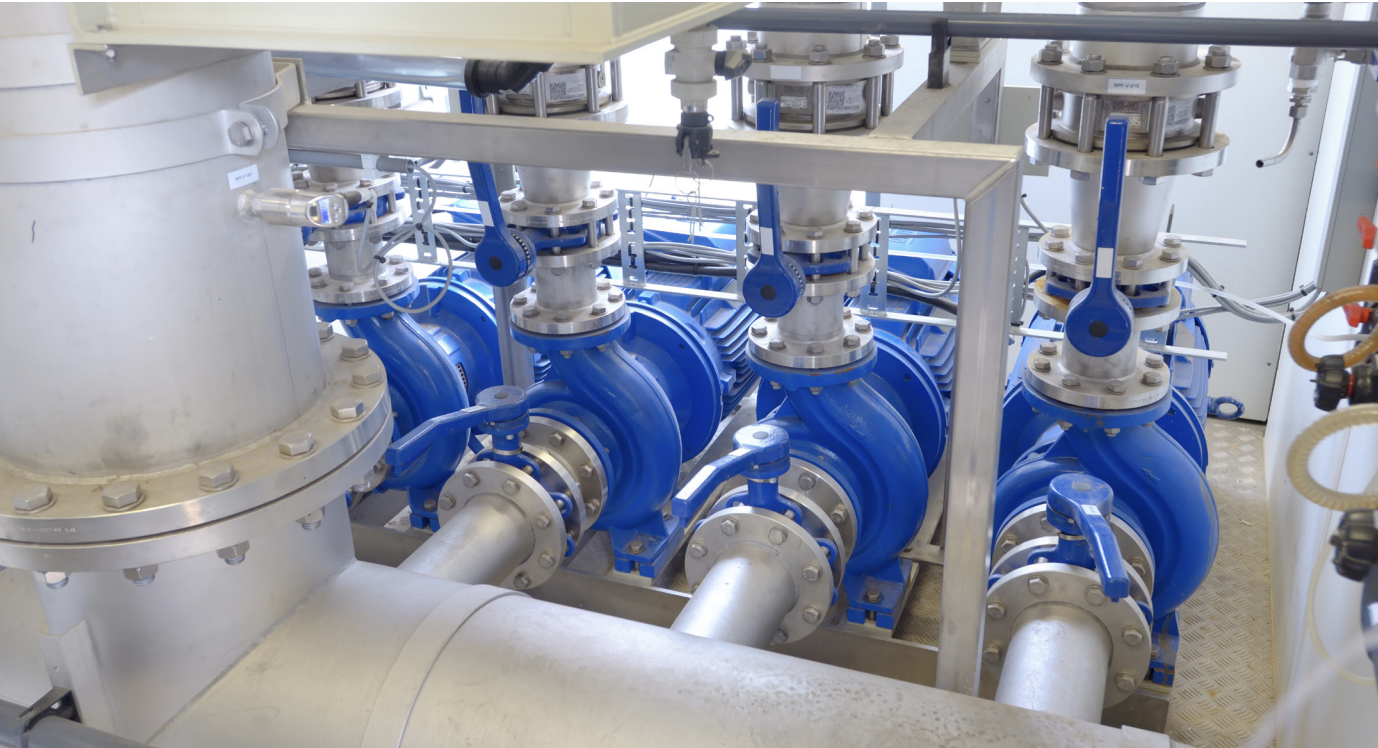
By Stormy Shaw
Across various industrial sectors projects to update and maintain proper water and wastewater processes are constantly underway. The trials and tribulations of outstanding industrial projects and honor of those successes are of high interest in these industries. You would expect the typical equipment refurbishment of equipment to keep things running but complete changes of processes and ingenuity in the face of a problem is a real challenge. When a facility decides to take a different approach to their normal processes it is important to protect all the new equipment to increase the quality and longevity it brings to the table.
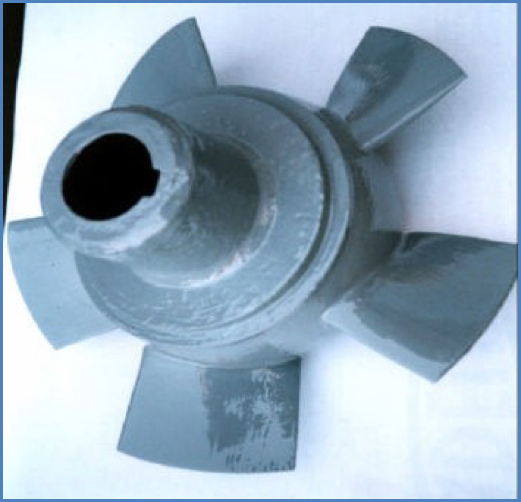
Wastewater Thermal Units
The addition or removal of thermal units from process chemical products is one of the greatest cost centers for the petro-chemical industry when transferring heat across metal. As is the case in heat exchangers, many factors influence the efficiency of the transfer. This is of primary concern to any large-scale operation, as it can translate to millions of dollars in savings or losses per year in fuel consumption costs.
A wastewater facility can potentially process millions of gallons of wastewater without significant equipment failure or shutdown. The removed water is taken to a centralized waste treatment facility to be discharged in compliance with a pretreatment permit. Data is then monitored to determine if additional technology could improve operations, particularly a reverse osmosis unit that could consolidate mineral content in a smaller volume of water to minimize disposal costs.
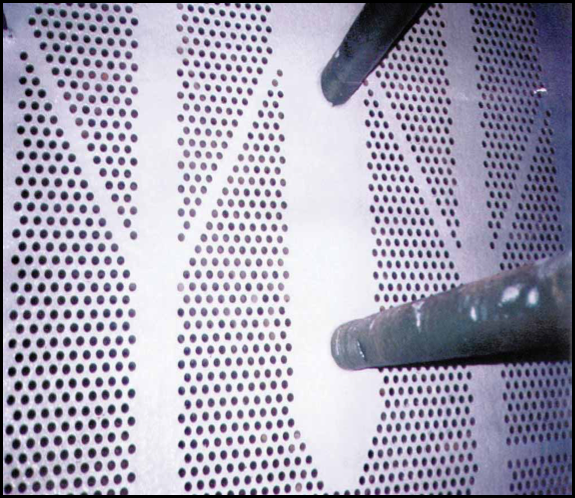
River Water Clarification
Propylene production facility materials are often used to food packaging, personal care products, medications and clothing. There is a means for cost savings by processing shale gas rather than purchasing ethylene and propylene from outside sources. However, the catch is that the science behind processing this gas requires a lot of water to keep the machinery cool.
Following a similar strategy in finding and processing from local sources, these plants can choose to pump water from the nearby rivers. The clean water allows the cooling system to be more effective and reduce the amount of downtime for the cleaning process each maintenance cycle. The reduction of maintenance downtime will reduce operation shutdown costs. The river water is treated with filtration systems that take out all heavy particles and produces clean water.
Once the job site is mobilized the facility can change the order in which they plan on building the tanks to facilitate other contractors being able to maintain their current construction paths. Once instillation is complete, tanks can perform well and the clarified river water will keep machinery cool during its manufacturing processes.
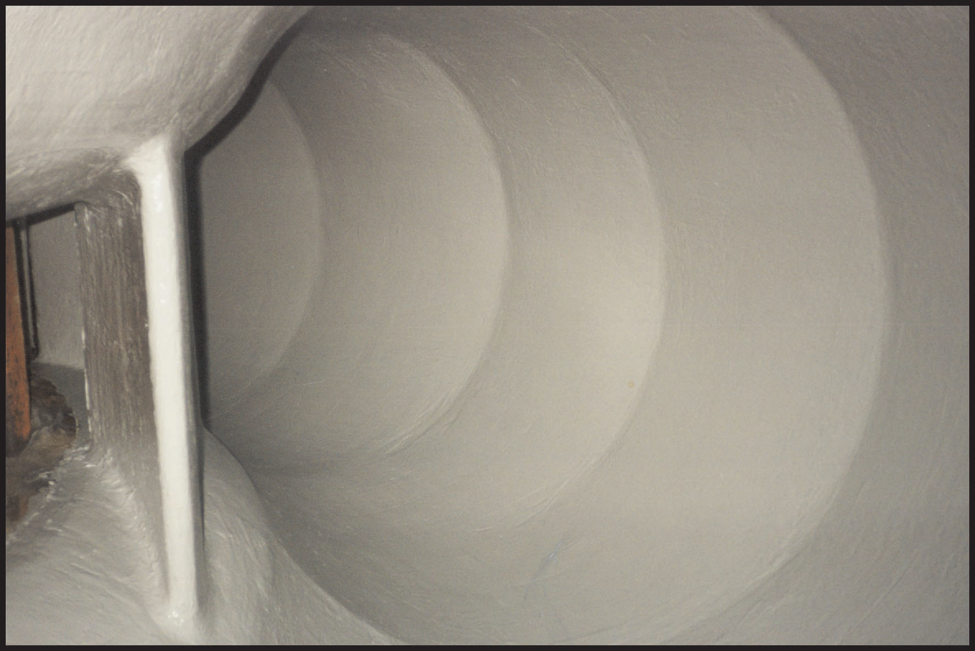
Renewable Energy Sources for Waste-to-Energy Plants
With a strain on local resources, growth cities may seek alternate means for energy. This growth can cause landfills for municipal waste to reach capacity. Building a waste-to-energy plant can reduce the amount of waste hauled to landfills and create a renewable energy source for the city’s wastewater treatment plants.
This innovative downdraft gasification plant can convert tons of waste, scrap tires and bio-solids per day into syngas, which is used to produce electricity for the wastewater treatment plant. The gasification plant’s process is projected to eliminate tons of carbon emissions and keep thousands of tons of wood, sludge and tires out of landfills each year. It also produces a carbon-rich biochar that can eventually be sold for profit.
Cities who decide to invest in this idea have found that the gasification plant has been very positive. Business and industry leaders make inquiries and visit the facility to investigate the process to reduce their carbon footprints and landfill volumes as well. This will garner positive media attention and reflects an ongoing commitment by the city to sustainable living. Residents often are found to be proud to be a part of a forward-thinking community that takes concern for the environment and lowering of energy costs is a bonus.
Improving Chemical Oxygen Demand in Wastewater
A petrochemical refining plant operator may have sought out a means to treat wastewater to improve chemical oxygen demand and biological oxygen demand. They may also want to remove free oil, total suspended solids and phenols for discharge into the sea. Large facilities may find this to be a costly project to complete. Despite the price tag, if this is deemed necessary at a facility there are other hang-ups such as design, need for a building to house controls, system components and chemical safety standards.
Capex and Opex costs may look high but compared to a conventional chemical treatment approach they are lower than anticipated, even with challenging site requirements including a building enclosure required to house plant components due to climate.
To overcome the challenge of reducing phenols and recalcitrant organisms, an existing oil separator should be optimized for free hydrocarbons and high level TSS removal. Specialized electrocoagulation, micro-bubble technology and used for phenols removal so the water could be discharged into local resources.
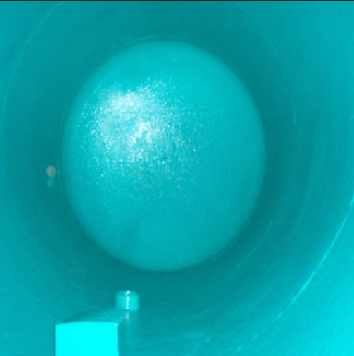
Power Plants Overcoming Terrain Obstacles
For some facilities, working with the terrain is necessary. If, for example, a power plant is constructed in the mountains but still requires water for cooling. This water will often be transported by a reservoir at and when using this water, the facility produces power. The water may travel across the terrain up to the water treatment plant and water tank, then down to the power plant. The water tank is higher than the power plant often to make the final transportation gravity fed.
The high lift and long distance of this type of water distribution system makes it vulnerable to surges and pipe breaks. This type of system requires a more stable flow. To achieve stability, the valve is designed to have manageable intervals for water control and protection in the event of surging. First, on the floating dock that pumps water, two surge-anticipating relief valves help relieve pressure from the pipe and last instillation of air valves on the pipeline to release air trapped in the pipe.
These valves can be opened before the surge comes and relieve the pressure from the pipe. This is especially important if there is a power failure and water rushes back down to the pump station. To anticipate these surges and avoid severe water hammer associated with power failure surges an additional installation of a control valve with a surge-anticipating relief valve mounted in a tee downstream of the pump check valve. Then, a pump control valve protects the pump that also can be used as a check valve when the flow returns.
In addition, to prevent cavitation damage, an installation of anti-cavitation technology. After the pressure reducing station, the water flows into the power plant with one last flow-regulating valve installed at the entrance gate to ensure stable flow and pressure.
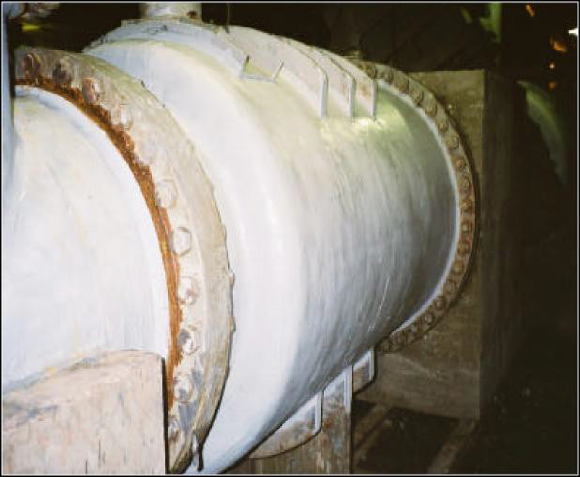