Case Studies
For over 20 years, USI has provided protective coatings and corrosion prevention products proven to protect our nations most critical infrastructure and industrial machinery. Along the way we have documented many projects and pain points we have been able to help our partners repair, protect and upgrade.
Most Recent Articles
Eliminating the Guesswork: Mastering Casing End Seals with Denso-Viscotaq
In the field, real-world conditions rarely match engineering drawings. Casing end seals are no exception. Pipes shift, measurements mislead, and unexpected gaps appear—especially under highways, railroads, or aging roadbeds where carrier pipes pass through thick-walled casings for structural support. Whether you’re working beneath I-75 in Lima, Ohio or navigating aging infrastructure beneath I-90/I-94 through Chicago, your sealing solution needs to adapt.
That’s where the Denso-Viscotaq™ Casing End Seal System shines—and why hands-on training is critical for your team.
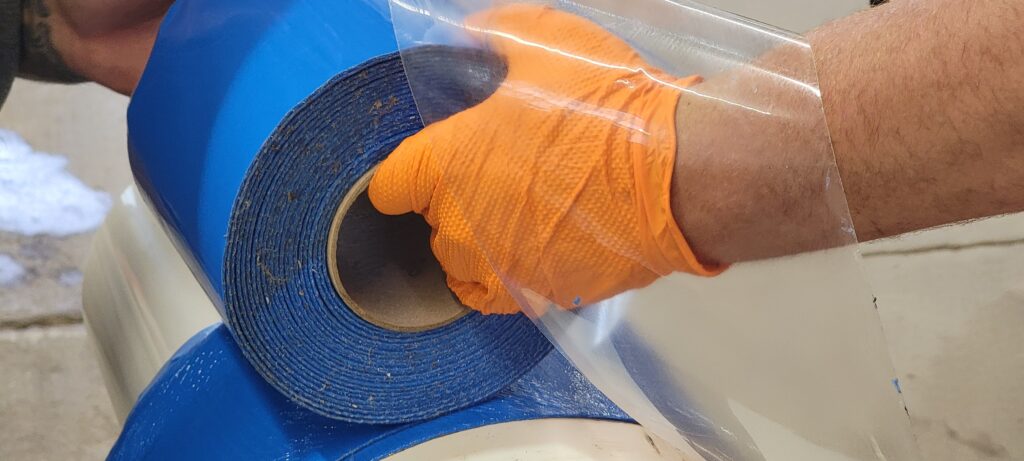
The Real-World Challenge
Casing end seals often fail for one simple reason: the unexpected. Pipes aren’t centered. Casing sizes don’t match drawings. Traditional seals can’t accommodate skewed angles or odd sizes—allowing water ingress and accelerating corrosion at one of the most vulnerable transition points in your pipeline.
These gaps expose your system to electrolytes and moisture, leading to corrosion, coating breakdown, and costly repairs.
The Field-Tested Solution
The Denso-Viscotaq System offers a flexible, durable, and easy-to-install solution that eliminates the need for perfect alignment. The system combines:
ViscoMastic™ packed into angular voids to displace air and moisture
ViscoWrap™ to provide continuous viscoelastic sealing across the interface
Denso Glass Outerwrap™ to deliver mechanical protection and durability
This layering not only boosts protection but also speeds up backfill and minimizes insurance costs by reducing open-ditch time.
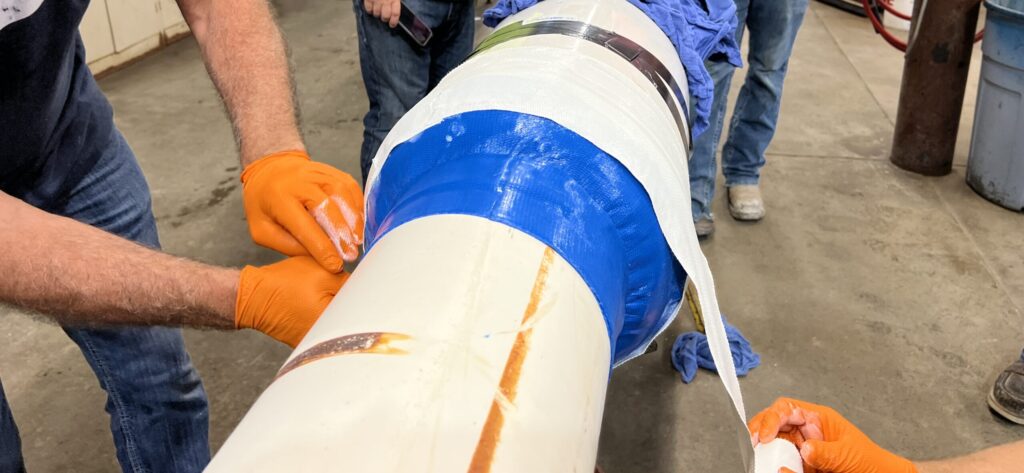
Why Training Matters
Every site is different. During a recent training beneath a highway crossing, one crew arrived expecting a 20″ carrier pipe in a 24″ casing—only to discover a 26″ casing. In another case, the casing was smaller than expected, making the prefabricated seals too loose. These are the challenges our training addresses.
Our Casing End Seal Training walks your crew through:
Assessing pipe and casing discrepancies
Field-friendly surface preparation
Proper application of mastic and wraps for varying conditions
Handling misalignments and non-standard geometries
Best practices for minimizing rework and ensuring long-term protection
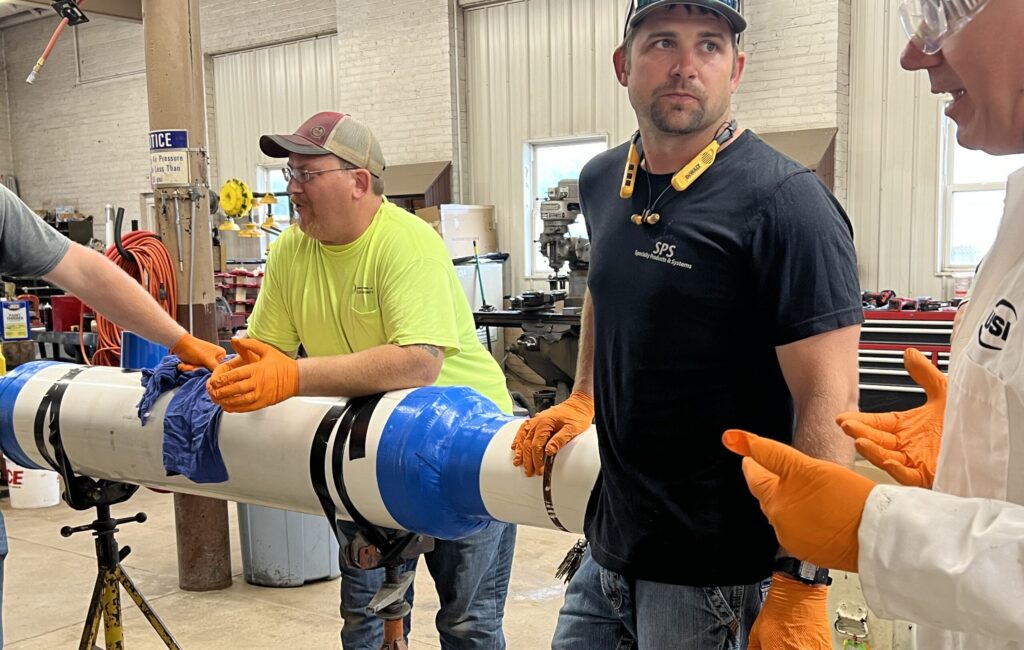
Book a Training Today
Whether you’re dealing with uncentered carrier pipes, outdated drawings, or high-risk environments, our Denso-Viscotaq Casing End Seal training equips your team to seal the deal—literally.
Get in touch today call us at 248-735-7000 or fill out the form below to schedule a session with our field experts and reduce your downtime, rework, and corrosion risk.
How to Plate Bond in 10 Minutes
These are the alternatives to avoid the hazards of hot work and allow you to repair structures and equipment that maybe there is not enough material to weld.
Plate bonding is a cold-applied composite repair method where a metal plate is permanently bonded over damaged or weakened areas of equipment using high-performance composite repair materials.
Why choose plate bonding over welding?
Avoid Hot Work Hazards
- No sparks, no flames, making it ideal for hazardous or flammable environments
- Eliminates need for hot work permits
Minimize Downtime
- Cold-applied, fast-curing systems get equipment back online faster
- With USI’s training, maintenance teams can complete the work without bringing in a certified welder
Stronger than welds in many situations
- Excellent adhesion and mechanical strength
- Distributes stress across the bonded area without heat distortion
- Non-corrosive
How it’s done – 5 Easy Steps
Surface Preparation – Substrate and Plate
- Degrease the surface using a suitable solvent like USI’s Universal Cleaner to remove oil, grease and contaminants.
- Mechanically abrade the area using an angle grinder fitted with a coarse pad or grinding disc. USI suggests a MBX bristle blaster for the best surface profile. You can also manually abrade the surface with a wire brush, sandpaper or metal file. Always follow the TDS for surface preparation.
- Remove all loose debris and clean again with solvent to ensure a clean bonding surface.
Dry Fit Check
- Position the plate over the damaged area and mark its placement
- Ensure proper alignment, surface contact and accessibility for application
Product Mixing
- Select the appropriate Resimac product based on the application (Resimetal 101, Resimetal 104 XF, Resimetal 106 XF)
- Mix the base and activator thoroughly until a consistent color and texture are achieved in the trio on the TDS.
Application
- Apply a uniform layer of mixed product to both the substrate and the back of the plate
- Use a trowel or spatula to ensure even coverage and eliminate air pockets
- Firmly press the plate into position, sliding slightly to seat the bond.
Clamping (if required)
- Apply mechanical pressure using clamps, weights or magnets to hold the plate in place during cure (especially for vertical or overhead surfaces)
- Maintain pressure according to cure time guidelines
Curing
- Allow the repair to fully cure before returning to service
- Cure time varies by product and environment but typically ranges from 6 to 24 hours
- For faster returns to service, optional heat curing may be used if appropriate
Final Inspection
- Verify bond integrity, inspect for gaps or voids, and test hardness (if required)
- Optional: Apply a protective topcoat or corrosion-resistant finish. Resimac has many different overcoat protection options, each tailored to a different environment. Make sure to talk to a USI expert technical advisor to get the right coating for your environment.
Make sure to view the video in its entirety to get the answers to the questions covered in the podcast:
- Can you use this system for load-bearing repairs?
- What are the most common mistakes when making plate bonding? How can they be avoided?
- What are the temperature limitations on this material?
- What are the labor time savings using plate bonding vs. hot work methods?
Unreliable Equipment Costing You Time and Money?
Unreliable Equipment Costing You Time and Money?
Get a FREE Consultation to Identify and Fix the Root Cause
Downtime, excessive energy costs, and unexpected equipment failures can cripple your productivity and profits. Our expert team of technical advisors is here to help you regain control.
What’s Included in Your Free Consultation?
Our experienced engineers will:
Assess your current maintenance processes for inefficiencies and bottlenecks
Identify potential failure points in critical systems and equipment
Provide hands-on support and training to strengthen your in-house team
The Benefits You’ll See:
Reduced unplanned downtime
Lower energy consumption
Safer, more efficient operations
Better trained, more confident maintenance staff
This is a no-pressure, no-obligation consultation. Just actionable insights and expert advice to help you get back on track.
Who Is This For?
Maintenance Managers
Plant Engineers
Operations and Production Leaders
If you’re responsible for keeping the plant running and costs down—this consultation is for you.
Book Your Free Consultation Today
It only takes a minute to schedule. Let’s uncover what’s holding your facility back and create a plan to fix it.
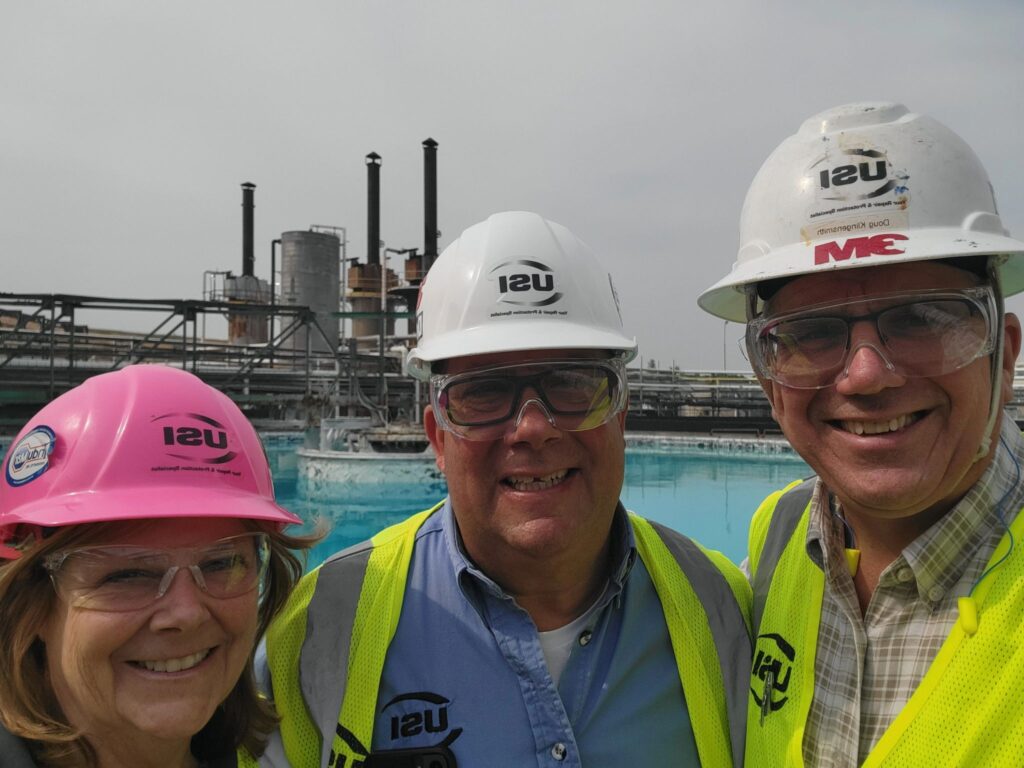