Why to Coat Concrete
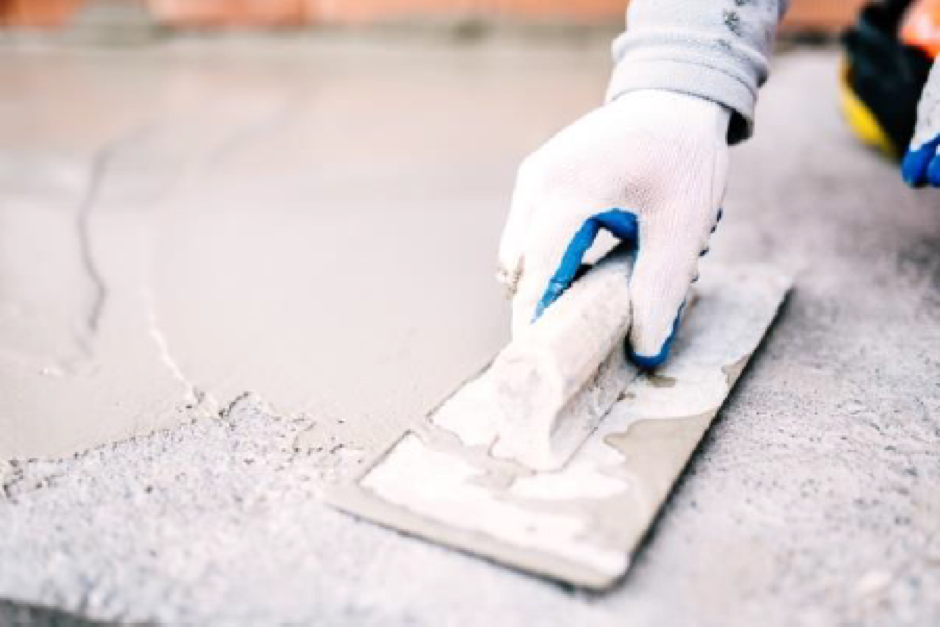
Concrete can be a difficult surface to coat because of its wide range of properties. Concrete is porous and uneven in texture, with differences in density from one section to another. If left unprotected, concrete floors can be exposed to several damaging elements, such as heavy traffic, chemicals, acids, cleaning products and food. This can cause a floor to become unsafe, unhygienic and unsightly. One way to prevent this from occurring is to coat the concrete with a construction resin.
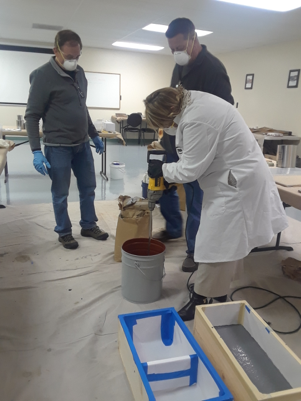
Aesthetics
As concrete is on of the most commonly used construction materials for both public and private buildings, it can be found in numerous facilities. However, because its natural color is a dull gray it is often seen as unattractive.
Flooring aesthetics pay a major role in the overall look and feel of a space and construction resins provide a solution that is aesthetically pleasing as well as functional. By choosing to coat there is no chipping or peeling, no oil or dirt staining, no discoloring when exposed to chemicals. Coatings offer excellent color and gloss retention or fading.
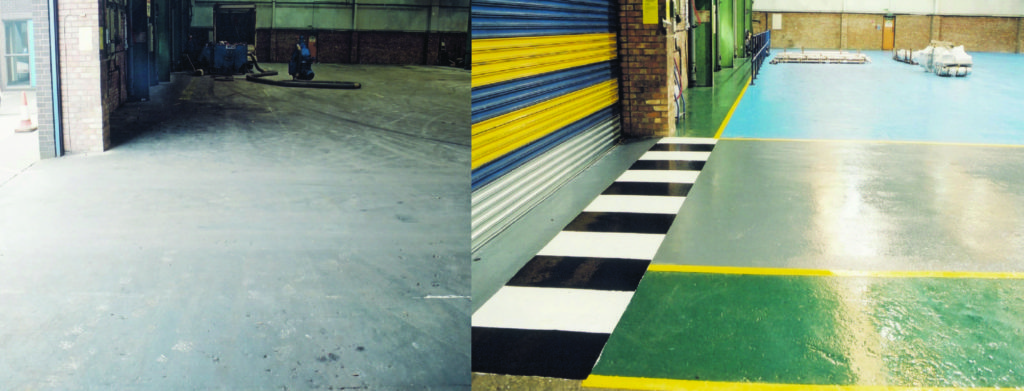
Chemical Resistance
Concrete floors can be exposed to several chemical and acids, depending on the environment. These chemicals and acids are damaging to unprotected concrete and over time will cause it to corrode and in some cases permanently stain. In areas where aggressive acids are being processed, the alkalinity of the concrete must be preserved by isolation from these acids with chemically resistant mortars, bricks, tiles or sheet membranes.
Before you can successfully coat a concrete structure, the natural properties of concrete must be understood. Concrete can be a simple mixture of Portland cement, lime, aggregate and water, but can also contain fillers selected for specific structural properties and resins selected for specific chemical-resistant properties, along with various additives selected to add specific strengthening properties to the otherwise simple mixture. Each variation creates a different surface with properties that can add or detract from a coating system’s ability to bond with the concrete.
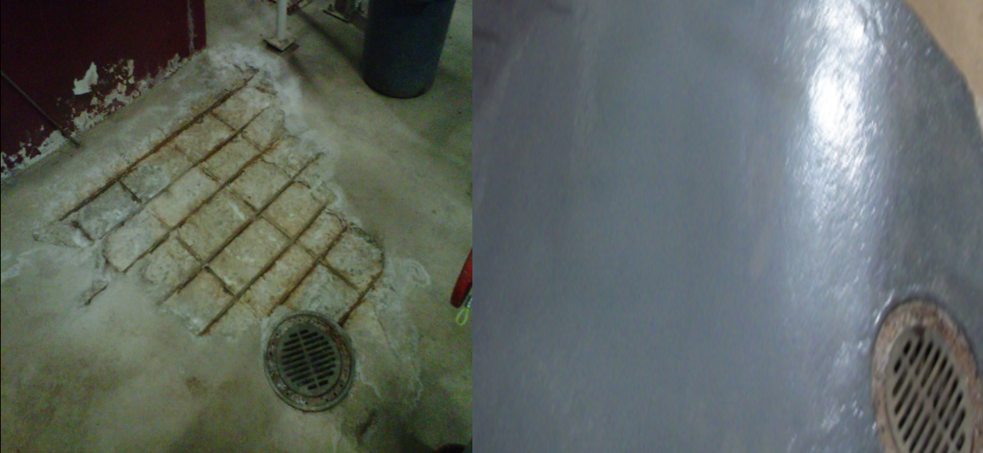
Fillers
There are many areas where conductive filler must be used in conjunction with organic polymers to dissipate static electricity. These and many other variations can be made to concrete to make it suitable for almost any location. Waterproofing additives can be used to seal joints and cracks to existing concrete, slip and skid resistant fillers can be added as well. UV stable abrasives can be added for a professional and long term solution.
Concrete is naturally alkaline, both in its curing stages and after its final cure. Therefore, any coating chosen must not only be able to withstand the environment that meets the concrete, but it must also be able to penetrate and bond with the alkaline surface of the concrete. Oil-based or alkyd coatings are unsuitable because the alkali in the concrete will react with the natural or synthetic oils in the coating, causing the creation of a sop-like film that leads to delamination of the coating from the concrete.
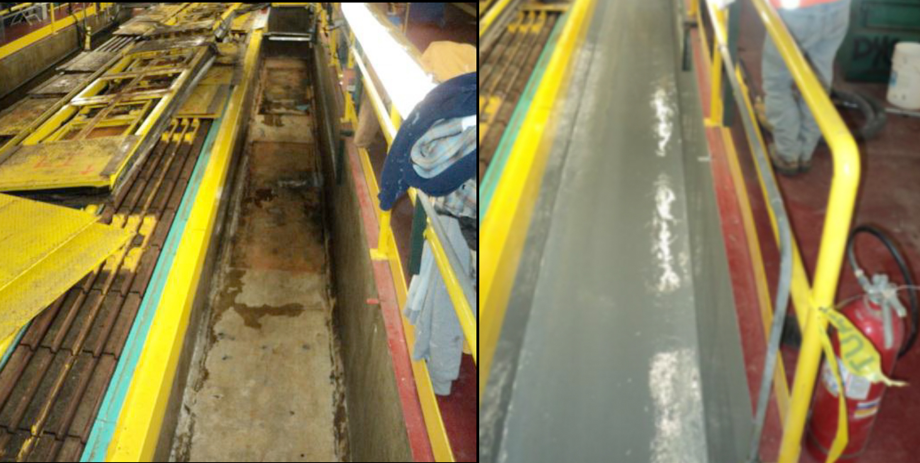
Porosity
The porosity of concrete allows moisture to penetrate it quite readily. Besides the problem of moisture intrusion, chloride penetration can attack the steel bars and mesh that are typically used for structural reinforcement. Since the corrosion products tend to occupy greater volume than the original steel, expansive stresses can crack or spall concrete, which has poor cohesive strength compared to its compressive strength. In northern climates, this porosity often leads to destruction of the concrete structure during freeze-thaw cycles. Coating concrete eliminates this problem and makes it much easier to clean. With this coating fixing the porosity the concrete is now flexible without cracking under heavy weight and resistant to weathering.
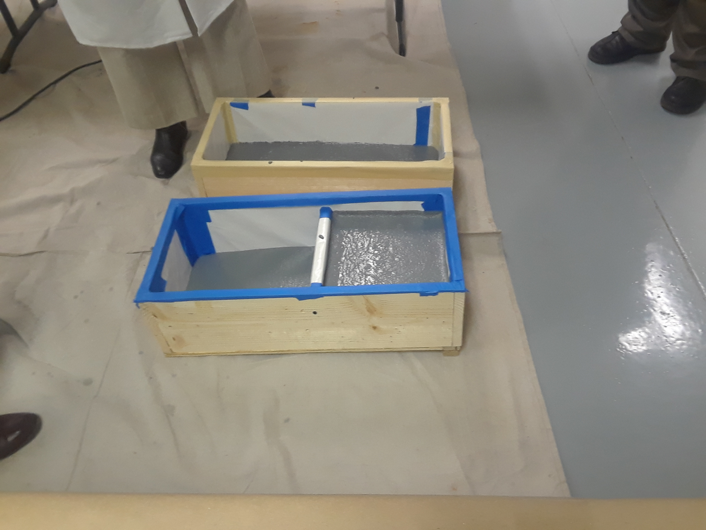
Decontamination
The normal porosity of concrete allows it to absorb almost any contaminant that meets it. Coating must render the concrete surface resistant to bacteria in many cases where food is involved. In these cases, many coating must resist growth of algae or other slime-type growths that could contaminate the food being processed.
Curing Mechanism
Regardless of the mix involved or the additives in the mix, concrete cures by a process of hydrolyzing water with the ingredients in the mix. The commonly used rule of thumb is that concrete needs 28 days to cure at an average temperature of 20 degrees C or 75 degrees F. It should be recognized that this traditional 28-day cure cycle allows the concrete to achieve the compressive strength designed into the mix ratio that was selected for the specific service conditions. Many coatings can be applied satisfactorily before the cure cycle is completed. This must be done in accordance with the manufacturer’s recommendations.
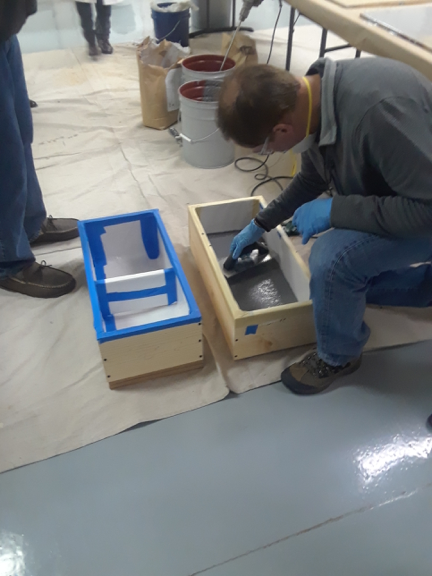
Sources:
Vincent, Louis D. “Coating Concrete.” Corrosion Basics, 3 Jan. 2017.
Top Five Reasons To Coat Your Concrete Floor
Armorthane Usa Inc. Corporate Office
https://www.armorthane.com/resources/news/transform-concrete.htm