Because of its exposure to the elements, the roof is the most vulnerable part of a building. UV exposure, wind, ice, rain and snow, extreme heat or cold can all take their toll on roofs and cause leaks or failures. Keeping a good roof over your head is very important with any building and there are chances that your roof can get damaged if you do not take proper care of it. You should always take care of your roof by keeping it in good condition. Unfortunately, many business don’t think of their roof until it fails.
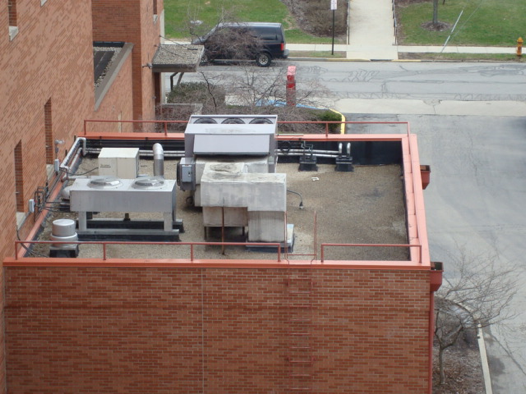
Restoration vs. Replacement
It’s commonly assumed that complete replacement is the best option for fixing and aging or leaking roof. In some cases, it is, but restoration is often a more desirable alternative. If a roof has failed it may be structurally unsound or if there is widespread damage replacement would be necessary. However, if the roof is only suffering from some damage, wear or other issues of exposure, restoration can be an alternative that would better work for you.
Roof replacement projects on industrial building are labor and resource-intensive and you can potentially run into the tens to hundreds of thousands of dollars on even moderate size buildings. Roof restoration generally comes in at a third of the cost or less of total replacement. Restoration requires fewer materials, man hours and involves maintenance rather than replacement, and is far less disruptive to regular business operations.
Even if your roof is not leaking it may require restoration to avoid damage costs. A way to tell is by checking for dryness, isolated splitting or cracks in the existing membrane, deteriorated flashings and other signs of minor wear like rust, missing fasteners, loosened or damaged panels. These signs should cause you to consider roof restoration. Deferred maintenance always result I added expense.
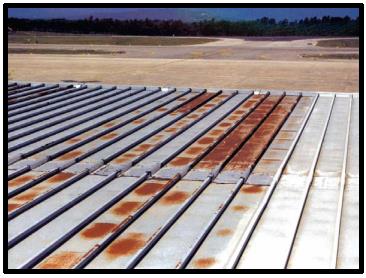
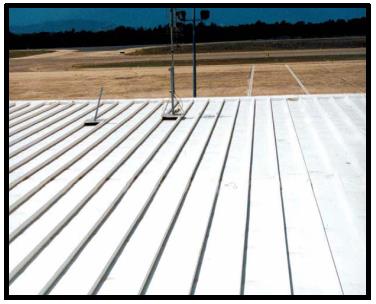
Steps to Take When Renovating
Many old style industrial roofs were coated in ethylene propylene diene terpolymer and are deteriorating, often to the point in some areas where the EPDM may be exposed and leaking. This will often happen with prolonged UV exposure. When this happens, it is important to inspect the area and find the locations where the insulation board below the coating is saturated. Removing and repairing those areas prior to coating is a must and then priming and coating the entire roof to follow.
When identifying the wet areas that need to be torn out and replaced, an infrared scan on the entire roof would be beneficial. The best time for this scan is dusk, after the sun has heated the roof all day. This is the time when the external temperature drops and the moisture is picked up by the infrared camera. This camera is accurate to about 12 inches and cuts out the guess work. The areas that are detected to be wet under the existing coating are easily detected when inspecting this way. Then you can mark the areas with spray paint or an alternate marking tool.
While removing the ruined insulation board it may also be beneficial to cut back the perimeter edge on the roof to relieve membrane shrinkage. Depending on design the edge may cause water collection and drainage issues if old and not edged properly. Metal detail may be more beneficial depending on the shape of the roof. The tear off the original coating and repairing of weaknesses in the roof many times will be more time consuming the actual coating application but it is worth the extra time spent to long term results.
With the old failing material removed, power washing or abrasive blasting would be the next step before replacing the insulation board. Once the new materials are in place, the rubber or polyuria is put back over the roof area and needs to be fastened down with either metal termination bars or other materials to provide a firm old and a tight seal. After this is when you would install edge detail. This task can be done with butyl tape or silicone caulk.
Once you have taken the steps listed you are ready to apply the coating. Which coating to use is dependent on the weather conditions in your area and how long you would like it to last.
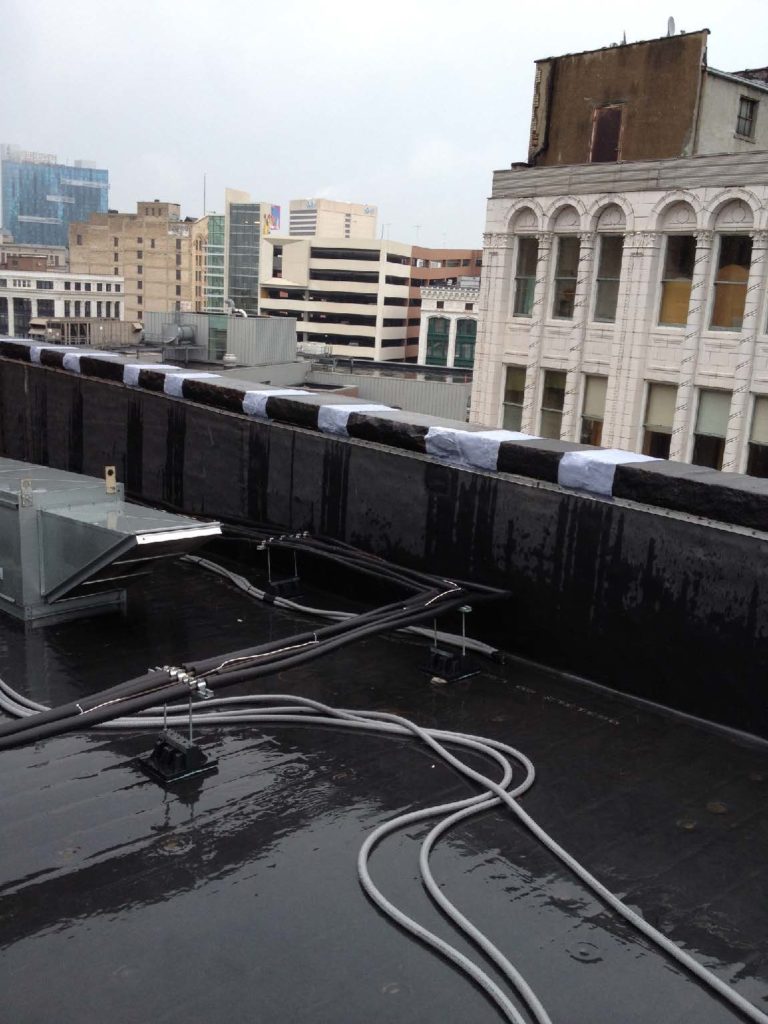
Gutters
Sometimes the roof itself will still be in fine shape but the gutters will be starting to corrode. Rather that replacement, repair would increase the life of the existing roof and gutter system. Box gutter systems require waterproofing and weatherproofing to avoid rusting. With immersion conditions preparations would require the area to be clean, dry and free of contamination prior to coating. A primer is recommended before waterproofing.
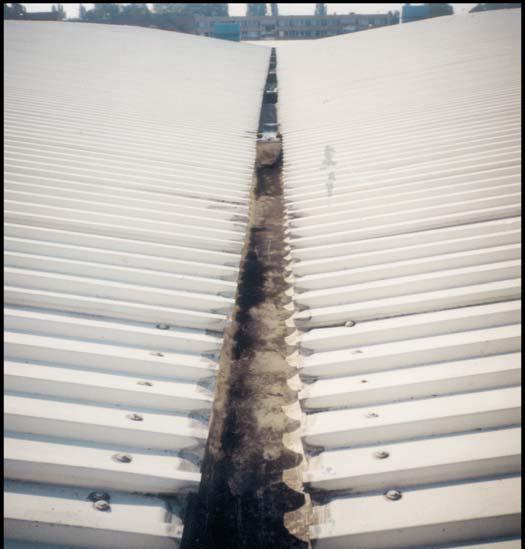
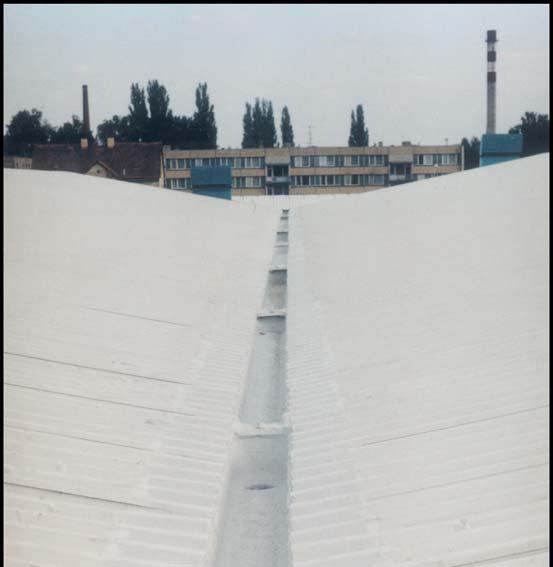
Contact Unconventional Solutions today to see what your best options for repairing instead of replacing your problem roof spots. Call us at 248-735-7000, email at cs@usigroups.com or fill out the contact form below.
Sources:
Frankes, Jennifer. “Speeding Toward Roof Renovation.” Coatings Pro, Jan. 2019.
“HOW TO RESTORE YOUR LEAKY COMMERCIAL ROOF.” Topps, 2019, www.toppsproducts.com/how-to-restore-your-leaky-commercial-roof.
“9 Roof Remodeling Tips to Know Before Starting Renovation.” ARS, 8 Feb. 2017, www.appliedroofingservices.com/blog/9-roof-remodeling-tips-know-starting-renovation/.