Learn how to repair, protect and upgrade your chillers with Unconventional Solutions. We review galvanic corrosion and how to repair it on your chiller.
Galvanic corrosion (dissimilar-metal corrosion) is an electrochemical process in which one metal corrodes preferentially, when in electrical contact with a different type of metal, and both metals are immersed in an electrolyte such as water. Chillers are prone to this type of corrosion, especially where the tubes meet up with the end plates. Unconventional Solutions offers several solutions to repair this type of corrosion on a chiller. Today we will review using Resimac products to repair a corroded chiller.
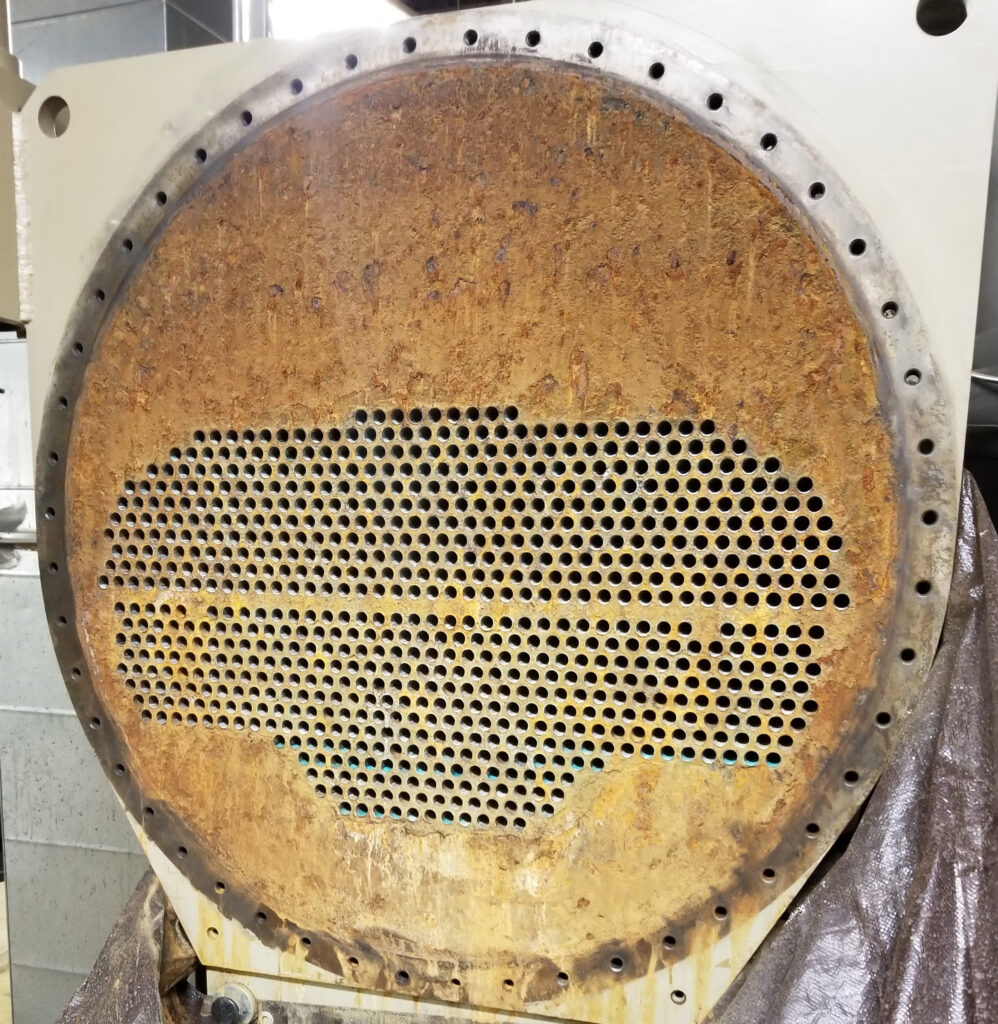
The first thing that needs to be done is to cork all of the tubes to prevent blast media and debris from entering the tubes. Once the tubes are corked, abrasive blast the area to NACE 2 specifications, to a 2 1/2 to 4 mil anchor pattern. This will ensure the best adhesion of the protective coating layer. 80% of coating failures are due to poor surface prep. To make sure that your corroded chiller repair lasts make sure to follow all surface prep instructions on your tech data sheet.
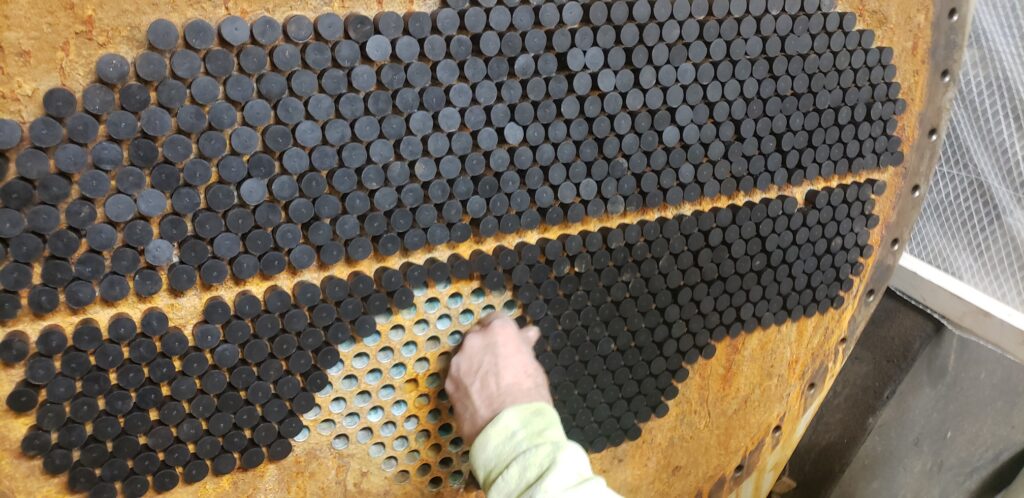
ResiMetal 101 Metal Repair Paste or ResiMetal 201 Ceramic Repair Paste is then used to rebuild lost metal around the tubes.
Lastly, two coats of ResiMetal 203 SuperFlow Ceramic Repair Fluid. First coat in Red. Second coat in Gray. That way as you do your regular maintenance checks on your chiller, if you start to see Red, you know it’s time to re-coat before you allow the galvanic corrosion to happen.
If you have more questions about repairing corroded chillers fill out the form below and Unconventional Solutions will reach out ASAP.