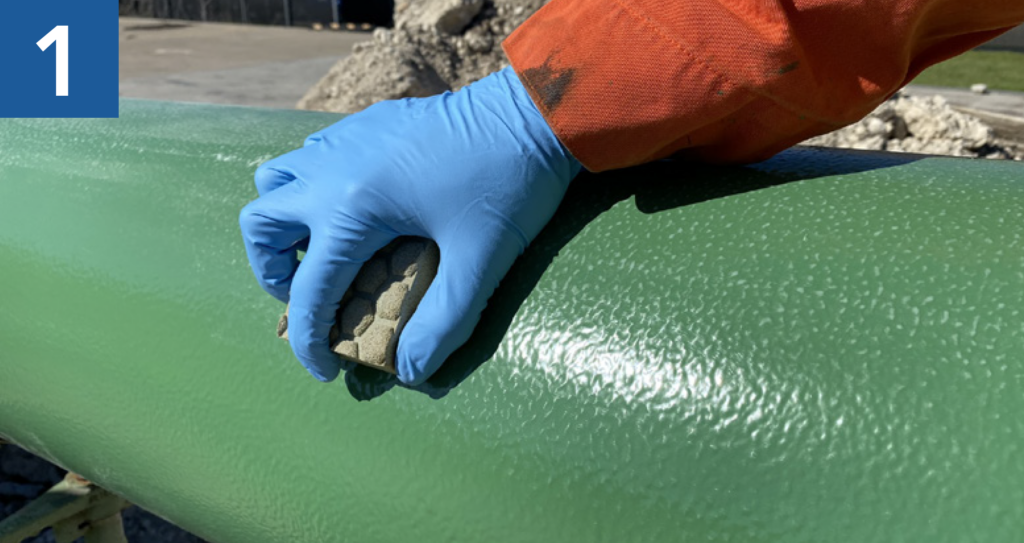
STEP 1
Prepare the area on either side of the field joint coating in accordance with SSPC SP1 “Solvent Cleaning”. Once the area is cleaned, roughen 6 inches of the mainline coating on each side of the field joint, using a coarse sandpaper (60 to 80 grit) or by brush blasting.
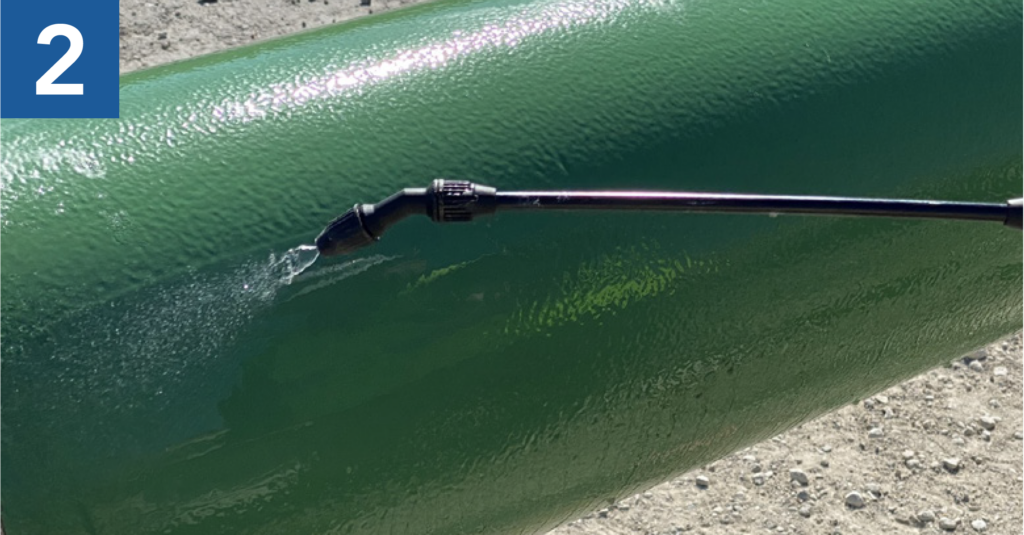
STEP 2
Wet the surface of the area that the roll will be applied onto using a water sprayer. Ethylene glycol or propylene glycol may be used when the temperature is near or below 32°F (0°C). Bore-Wrap is water activated, it is necessary that water is continuously sprayed onto the surface and underbelly of the roll as it is being applied.
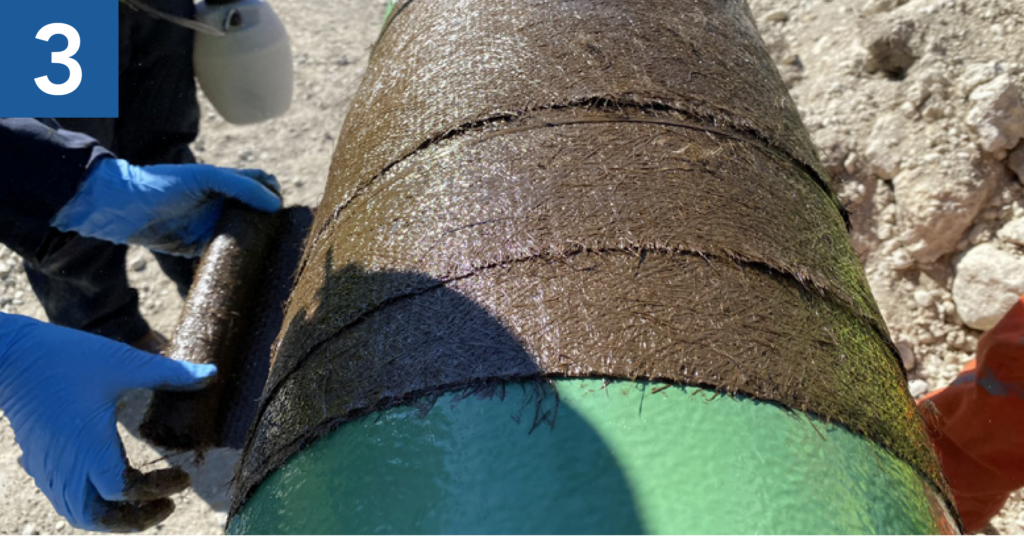
STEP 3
Begin wrapping 6″ (150 mm) in front of the field joint coating, with the Omni-directional matting surface facing out “chop on top”. The woven structured (checker board) side of the fiber is to be placed facing the surface of the pipe. Wrap the material circumferentially to begin, ensuring that the leading edge has a minimum of 2 layers. Then proceed across the field joint wrapping with a minimum of 50% overlap until the wrap has extended 6″ (150 mm) beyond the field joint coating. Then do a final wrap around circumferentially and end with the fiber on top of fiber (do not leave a single layer hanging from the back).
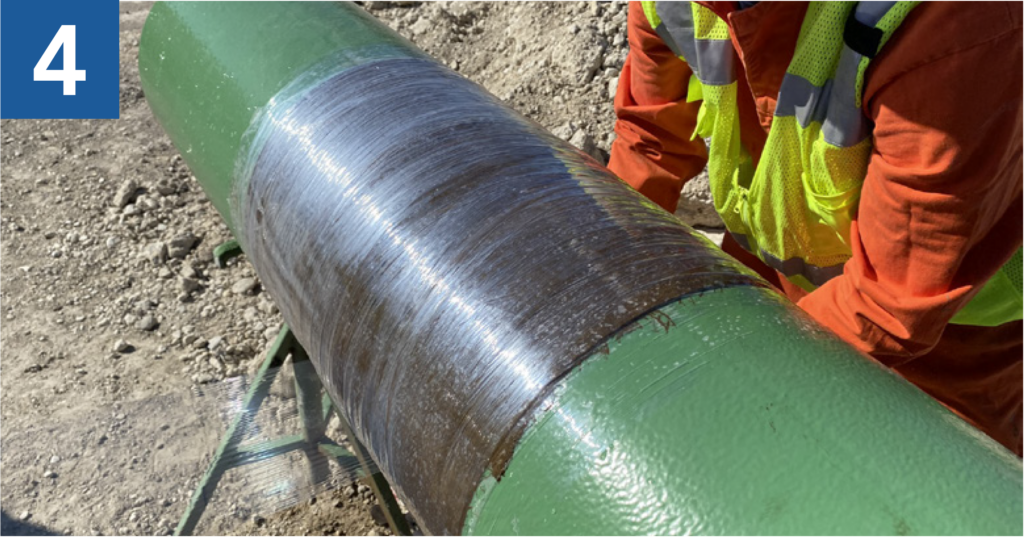
STEP 4
Ensure the wrap is completely saturated and then immediately begin wrapping Denso Poly-Wrap over the Bore-Wrap quickly and with tension applied. Overlap each end of the Bore-Wrap by at least 2″ (50 mm) to ensure the ends lay flat and the resin can be retained. 2 to 3 passes should suffice.
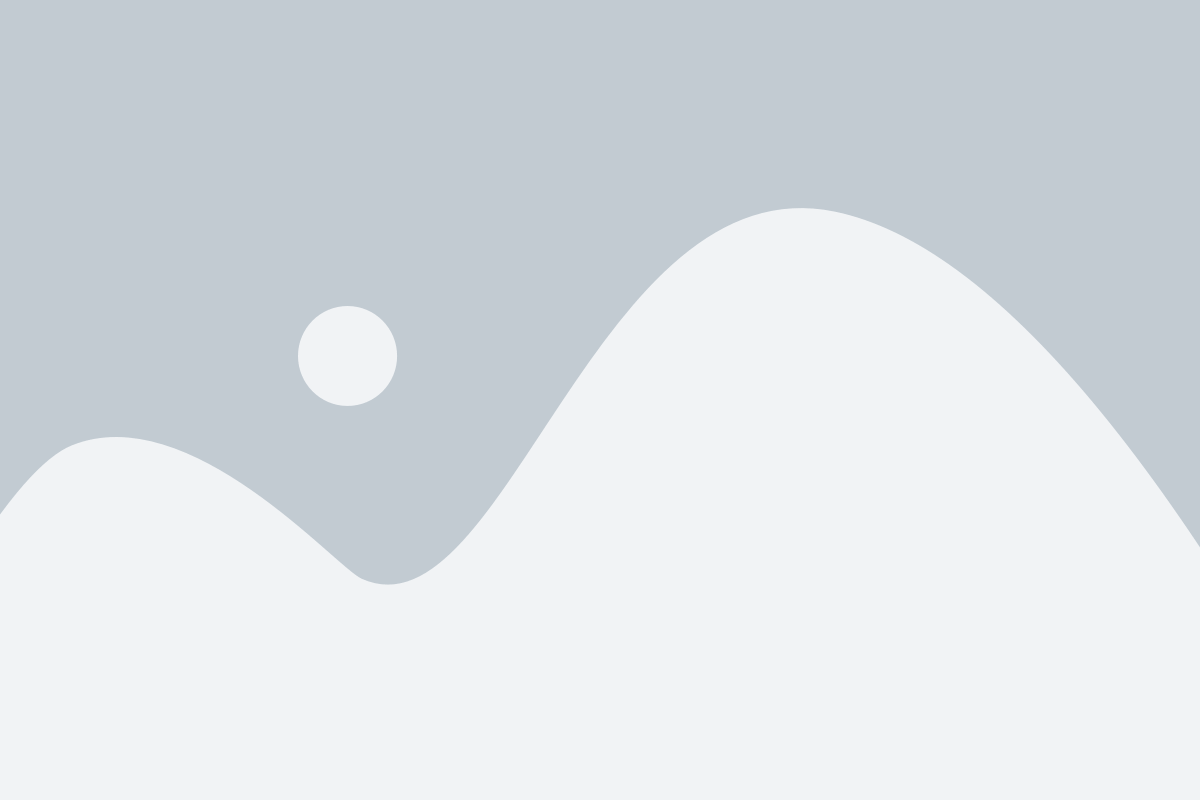
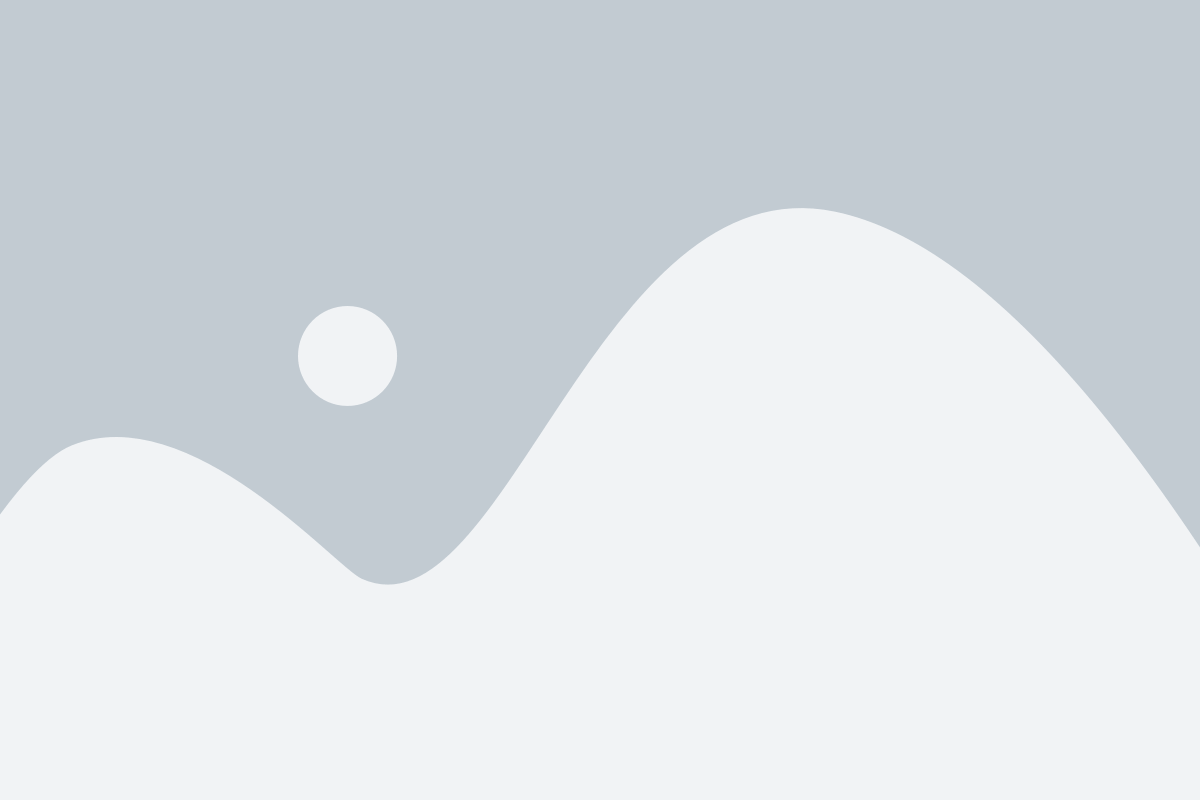
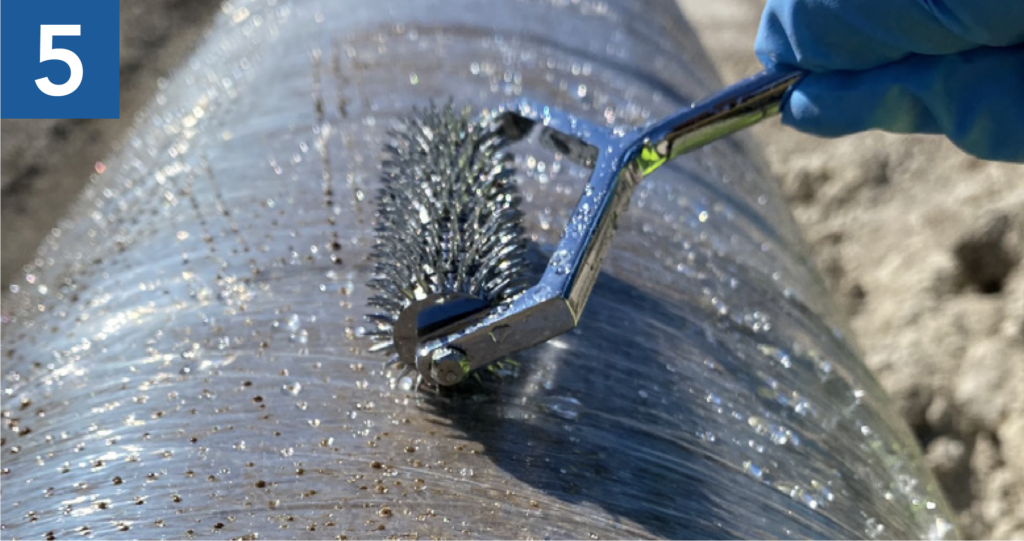
STEP 5
Once fully compressed, use Denso’s perforating tool to puncture the Denso Poly-Wrap. This will allow for excess resin, moisture, and CO2 from the reaction to escape. Perforate using enough pressure to get through the Denso Poly-Wrap but not through the layers of Bore-Wrap.

STEP 6
Allow the roll to remain under compression while it cures. Resin may have escaped through the perforations, that resin is a fair indicator of the materials dry to touch time. Once the material has fully cured the Denso Poly-Wrap may be removed. Cure can be checked by using a Shore D gauge on a high point of the resin (avoid measuring near ridges and fibers as the gauge tip can move). The product is ready to be used at a Shore D of 65 or greater.
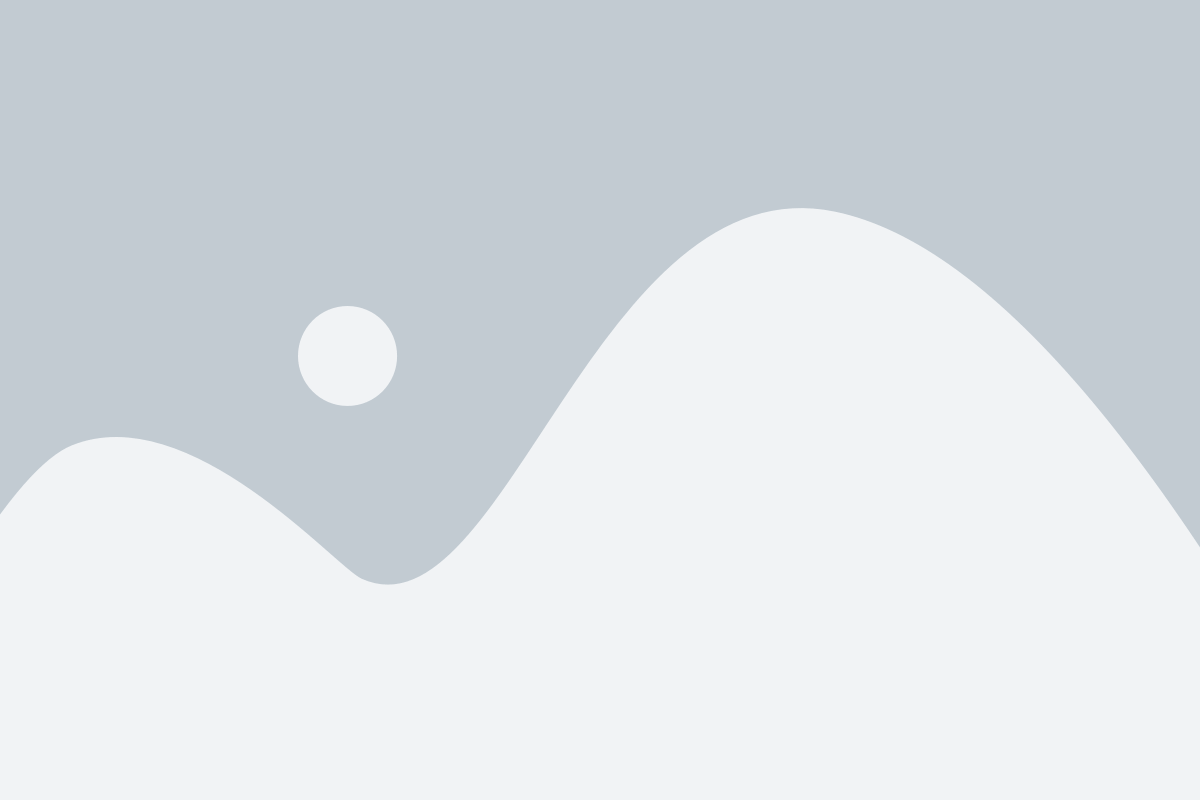
Training helps you keep projects on time and under budget.
The Unconventional Solutions USI Team has AMPP Certified Coating Inspectors on staff and can train in the preparation, mixing and application of Denso, 3M or SPC pipeline coatings. Let the USI Team help you and your team get it right the first time and avoid the cost and time of re-coating. Our Certified Coating Inspectors have over 50 years of coating know-how. We can not only get you and your team certified, but we can share our experience to ensure a smooth coating application from start to finish.
USI has 4 certified Denso Trainers, also an SPC Certified Trainer, and two 3M™ Scotchkote™ Trainers along with 2-AMPP (formerly NACE) Senior Coating Inspectors (CIP-3) and our owner Tiffany is an AMPP Coating Inspector (formerly NACE CIP-2 Coating Inspector)
Call us to schedule today: 248.735.7000