When selecting materials to deal with atmospheric corrosion, engineers have to balance three different objectives:
- Capital cost
- Operation and maintenance costs
- Functional conditions the material must operate in, yet still have acceptable attributions
Stainless steel is the obvious answer, but for entire systems, it can become cost prohibitive. So a cost effective answer would be to use carbon steel instead and protect it from the environment with a protective coating.
THE PROBLEM:
Maintaining many operating assets in an environment is expensive and challenging. Imagine you are a terminal operator with 30 terminals, each with 10 tanks each. If each tank had to be recoated every 20 years, that’s around 15 tanks being recoated a year. But which ones would you coat first? Can you over coat, or must you remove the coating systems completely and restart from scratch? What products, which contractors, what is the expectation of coating performance?
The first step is understanding the condition of all the assets, so the work can be specified and planned. Starting your program off with coating condition assessment allows the operator to:
- Gather information for developing a detailed scope of work for specification purposes
- Provide a basis for budgeting for maintenance, and quantify spending
- Gain information to prepare a multi-year program to maintain the asset
Other information condition surveys can provide include:
- Information on coating performance
- Warranty and premature failure
WHAT TO LOOK FOR IN A COATINGS ASSESSMENT:
Coating surveys quantify the key items that must be budgeted for including all coated surfaces, and may also include concrete, joint sealants, composites, and hard-to-coat areas. Information needed includes:
- Coating thickness
- Coating adhesion
- Quantity of corrosion
- Hazardous material identification
- Operational requirements
- Area layout/staging
Condition surveys provide information on the ‘what, where, and how’ but often owners and engineers focus on the coating product itself to determine whether the corrosion control system performs to specifications.
ADDING COATING CONDITION ASSESSMENTS INTO CORROSION MANAGEMENT PROGRAM
A good corrosion management program starts with a coating condition survey to understand which direction you’re going in. Once you analyze the findings of the assessment, you can perform a quality specification. Ensuring the right material is used, over the right surface preparation and under the right conditions, is critical to coating performance. These must occur simultaneously to get the intended effect. All this leads to an overall reduction of operating costs and maximize the terminal’s lifespan.
CONCLUSION
Operators must have an effective corrosion management program to reduce costs and protect their systems. Start with a coatings condition survey and incorporate each quality assurance element to yield the best results. Each step in the process is critical and building on the foundation of the assessment allows for proactive, appropriate action.
—-
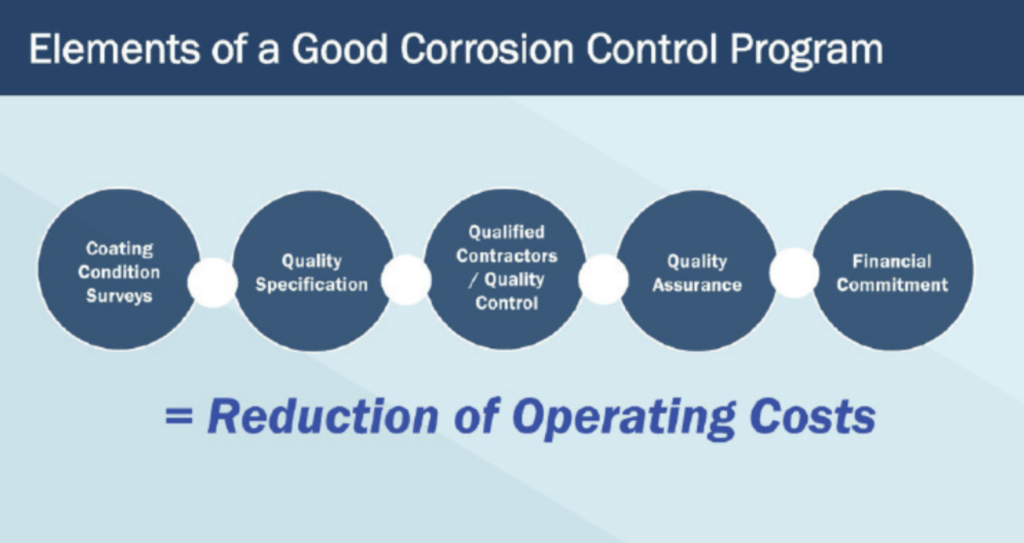
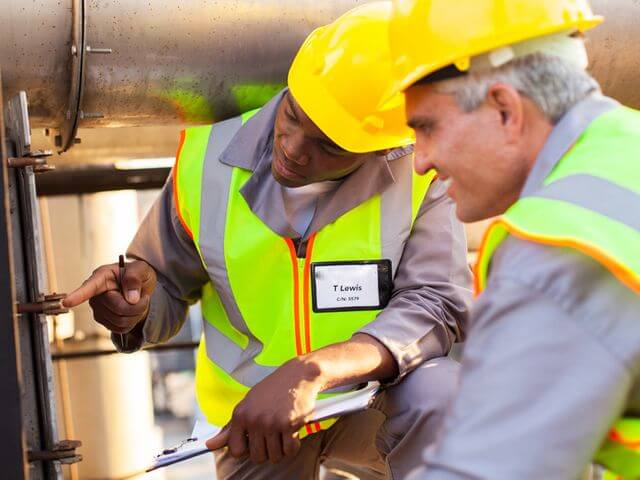
How Is a USI Coating Condition Survey Conducted?
A coating survey is designed and carried out with planning, recording and reporting. It’s essential for USI Group to conduct coating surveys using a methodical and structured approach. This ensures that each client’s survey benefits from the same rigorous standards. The following steps form the core of a coating condition survey.
Contact an Unconventional Solutions Coating expert to learn more about Coating Condition Surveys.
- Define the parameters of the survey before the survey is started
- Determine what is the expected output of the survey
- Assess and recognize current grading conditions
- Assess corrosive environmental issues and current conditions
- Assess the current coating conditions, date of application, the coating manufacturer, the applicator, etc.
- Note extraordinary events and occurrences (ie. weather conditions, fire, maintenance, repairs, etc.)
- Assess the existing coating, considering adherence to the structure, dry film thickness, the percentage of failure
- PLAN THE NEXT STEPS